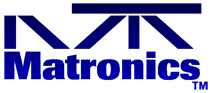 |
Matronics Email Lists Web Forum Interface to the Matronics Email Lists
|
View previous topic :: View next topic |
Author |
Message |
nuckolls.bob(at)aeroelect Guest
|
Posted: Mon Oct 12, 2009 6:32 am Post subject: Diodes vs. Bi-Directional Zeners for Contactors |
|
|
At 06:20 AM 10/12/2009, you wrote:
Quote: | I'm building a new power grid for a customer and the research on contactors ended up with some digging on the diodes that we use across the coils of the contactors, and whether they're necessary. We're using a couple Tyco Kilovac EV200s and since they have pigtail wires instead of terminals, it's tougher to install the diodes. Tyco says we don't need "back EMF protection" with the EV200s. |
EV200's have internal electronics that take care
of the mag-field collapse spike from the contactor's
coil.
Quote: | But we are also using the LEV100 contactors, which do need the back EMF protection.
Tyco has a couple documents that explain the various methods to handle the back EMF.
http://relays.tycoelectronics.com/appnotes/app_pdfs/13c3311.pdf
http://relays.tycoelectronics.com/appnotes/app_pdfs/13c3264.pdf
Eric at Perihelion Design sells SnapJacks, and claims that they are superior to using diodes. Eric's claims match up with the information in the Tyco documents. Both Eric and Tyco claim that bi-directional zeners have all the advantages of protecting the switch without slowing down the contact separation speed, which decreases contactor life. |
Which is all demonstrable BS. Even the authors of the
Tyco documents correctly observe that "tight" coil
suppression of a plain diode causes contactor OPENING
DELAY and then incorrectly extend that observation
into a reduction of CONTACT SPREADING VELOCITY which
would indeed increase the duration of arcing during
opening.
Plain diodes have been used by the hundreds of
thousands on TC aircraft for over 40 years and
they are still meeting the design goals of the
system designers today. Further, papers like
those on the Tyco site speak to relay life
on the order of hundreds of thousands of cycles.
Their research into contact life vs. coil suppression
techniques will be based on laboratory
cycle testing (Hey Joe! Lookit here! That evil coil
suppression technique kicked our service life
in the head . . . instead of 110,000 cycles we
only got 95,000 cycles.)
The contactors in the average light plane
won't get 5,000 cycles over the LIFETIME
of the airplane.
Use what ever coil suppression technique
gives you warm fuzzies but know too that the least
expensive and simplest technique is fine.
Quote: | One concern I have is the failure modes of diodes and bi-directional zeners. If they fail open, no big deal, but if either has a failure mode that would create a short, that could cause problems. |
What problem? Suppose your contactor fails to
close for any one of many other reasons? Are any of
these contactors used in a manner where failure
puts outcome of flight at risk? If so, you need to craft
a Plan-B to deal comfortably with that failure. May I suggest
that your worries about forestalling failure by
judicious selection of coil suppression is a
distraction. You should ASSUME that the contactor
will be unavailable to you at some time in the
future . . . now, what alternatives are in place
to deal with that failure? See chapter 17 of the
'Connection.
Quote: | I read somewhere that high voltage tends to result in a short failure, but high amperage results in an open failure. There's no circuit protection on these coils (except for the starter). |
The ENERGY dissipated in ALL coil suppression
is very short duration (milliseconds per flight
cycle) and perhaps 1,000th the rated capability
of the device. They don't fail except for reasons
of manufacturing defect or installation error . . .
and particularly NOT from having selected the wrong
rating for the device. When a coil suppression device
is working, the VOLTAGE and CURRENT impressed upon
it is trivial compared to its ratings.
Quote: |
I'm interested in comments on the relative merits of using diodes vs. bi-directional zeners. Also, the failure modes of both devices. And how to size the bi-directional zeners to minimize the chance of a failure, especially a short failure.
|
You're worrying waaaayyyy too much about it.
This topic has been discussed and many platinum
plated coil suppression techniques have been offered
up as the path to Nirvana. But when it gets down
to the physics of contactor and power relay
control, it's easy to demonstrate.
http://www.aeroelectric.com/Pictures/Curves/704-1OpeningTimeNoDiode.gif
http://www.aeroelectric.com/Pictures/Curves/704-1OpeningTimeWithDiode.gif
http://www.aeroelectric.com/Pictures/Curves/704-1DelayWithDiode.gif
http://www.aeroelectric.com/Pictures/Curves/7041DelayWithDiode.gif
http://www.aeroelectric.com/Pictures/Curves/CH_w_1n5400.gif
http://www.aeroelectric.com/Pictures/Curves/CH_w_2x18v_Transorbs.gif
http://www.aeroelectric.com/Pictures/Curves/CH_w_120_Ohm.gif
http://www.aeroelectric.com/Pictures/Curves/S704-1_Drop-Out_Delay_with_Diode.jpg
http://www.aeroelectric.com/Pictures/Curves/S704-1_Drop-Out_Delay_without_Diode.jpg
These are but a few of dozens of traces recorded by
myself where we looked at drop-out-delay, contact
transition velocity, and contact bounce vs. various coil
suppression techniques (including simple placement
of a 120 ohm resistor across the coil!).
Bottom line is that anything you want to do will
be fine . . . make it easy on yourself and be wary
of pronouncements and dire warnings from folk who
not been there nor done that. Do a failure mode
effects analysis and craft architectures that offer
a Plan-B for ALL uncomfortable failures. The road
to comfortable termination of flight is not paved with
prophylactics AGAINST failure . . . rather a PLAN for
dealing comfortably with any failure.
Bob . . . [quote][b]
| - The Matronics AeroElectric-List Email Forum - | | Use the List Feature Navigator to browse the many List utilities available such as the Email Subscriptions page, Archive Search & Download, 7-Day Browse, Chat, FAQ, Photoshare, and much more:
http://www.matronics.com/Navigator?AeroElectric-List |
|
|
|
Back to top |
|
 |
mikeeasley(at)aol.com Guest
|
Posted: Mon Oct 12, 2009 7:16 am Post subject: Diodes vs. Bi-Directional Zeners for Contactors |
|
|
Bob,
So I believe there's a decent argument to do nothing. If the spike is small, and the switches are robust enough to handle far more than the spike, and the current through the contactors is far below the contactor rating, and the number of cycles of the switch and the contactor are far below the advertised life...
...then leaving off the diodes is a viable alternative.
Mike Easley
In a message dated 10/12/09 08:33:46 Mountain Daylight Time, nuckolls.bob(at)aeroelectric.com writes:
Quote: | .aolmailheader {font-size:8pt; color:black; font-family:Arial} a.aolmailheader:link {color:blue; text-decoration:underline; font-weight:normal} a.aolmailheader:visited {color:magenta; text-decoration:underline; font-weight:normal} a.aolmailheader:active {color:blue; text-decoration:underline; font-weight:normal} a.aolmailheader:hover {color:blue; text-decoration:underline; font-weight:normal} At 06:20 AM 10/12/2009, you wrote:
Quote: | I'm building a new power grid for a customer and the research on contactors ended up with some digging on the diodes that we use across the coils of the contactors, and whether they're necessary. We're using a couple Tyco Kilovac EV200s and since they have pigtail wires instead of terminals, it's tougher to install the diodes. Tyco says we don't need "back EMF protection" with the EV200s. |
EV200's have internal electronics that take care
of the mag-field collapse spike from the contactor's
coil.
Quote: | But we are also using the LEV100 contactors, which do need the back EMF protection.
Tyco has a couple documents that explain the various methods to handle the back EMF.
http://relays.tycoelectronics.com/appnotes/app_pdfs/13c3311.pdf
http://relays.tycoelectronics.com/appnotes/app_pdfs/13c3264.pdf
Eric at Perihelion Design sells SnapJacks, and cla ims that they are superior to using diodes. Eric's claims match up with the information in the Tyco documents. Both Eric and Tyco claim that bi-directional zeners have all the advantages of protecting the switch without slowing down the contact separation speed, which decreases contactor life. |
Which is all demonstrable BS. Even the authors of the
Tyco documents correctly observe that "tight" coil
suppression of a plain diode causes contactor OPENING
DELAY and then incorrectly extend that observation
into a reduction of CONTACT SPREADING VELOCITY which
would indeed increase the duration of arcing during
opening.
Plain diodes have been used by the hundreds of
thousands on TC aircraft for over 40 years and
they are still meeting the design goals of the
system designers today. F urther, papers like
those on the Tyco site speak to relay life
on the order of hundreds of thousands of cycles.
Their research into contact life vs. coil suppression
techniques will be based on laboratory
cycle testing (Hey Joe! Lookit here! That evil coil
suppression technique kicked our service life
in the head . . . instead of 110,000 cycles we
only got 95,000 cycles.)
The contactors in the average light plane
won't get 5,000 cycles over the LIFETIME
of the airplane.
Use what ever coil suppression technique
gives you warm fuzzies but know too that the least
expensive and simplest technique is fine.
Quote: | One concern I have is the failure modes of diodes and bi-directional zeners. If they fail open, no big deal, but if either has a failure mode that would create a short, that could cause problems. |
What problem? Suppose your contactor fails to
close for any one of many other reasons? Are any of
these contactors used in a manner where failure
puts outcome of flight at risk? If so, you need to craft
a Plan-B to deal comfortably with that failure. May I suggest
that your worries about forestalling failure by
judicious selection of coil suppression is a
distraction. You should ASSUME that the contactor
will be unavailable to you at some time in the
future . . . now, what alternatives are in place
to deal with that failure? See chapter 17 of the
'Connection.
Quote: | I read somewhere that high voltage tends to result in a short failure, but high amperage results in an open failure. There's no circuit protection on these coils (except for the starter). |
The ENERGY dissipated in ALL coil suppression
is very short duration (milliseconds per flight
cycle) and perhaps 1,000th the rated capability
of the device. They don't fail except for reasons
of manufacturing defect or installation error . . .
and particularly NOT from having selected the wrong
rating for the device. When a coil suppression device
is working, the VOLTAGE and CURRENT impressed upon
it is trivial compared to its ratings.
Quote: |
I'm interested in comments on the relative merits of using diodes vs. bi-directional zeners. Also, the failure modes of both devices. And how to size the bi-directional zeners to minimize the chance of a failure, especially a short failure.
|
You're worrying waaaayyyy too much about it.
This topic has been discussed and many platinum
plated coil suppression techniques have been offered
up as the path to Nirvana. But when it gets down
to the physics of contactor and power relay
control, it's easy to demonstrate.
http://www.aeroelectric.com/Pictures/Curv es/704-1OpeningTimeNoDiode.gif
http://www.aeroelectric.com/Pictures/Curves/704-1OpeningTimeWithDiode.gif
http://www.aeroelectric.com/Pictures/Curves/704-1DelayWithDiode.gif
http://www.aeroelectric.com/Pictures/C urves/7041DelayWithDiode.gif
http://www.aeroelectric.com/Pictures/Curves/CH_w_1n5400.gif
http://www.aeroelectric.com/Pictures/Curves/CH_w_2x18v_Transorbs.gif
http://www.aeroelectric.com/Pictures/Curves/CH_w_120_Ohm.gif
http://www.aeroelectric.com/Pictures/Curves/S704-1_Drop-Out_Delay_with_Diode.jpg
http://www.aeroelectric.com/Pictures/Curves/S704-1_Drop-Out_Delay_without_Diode.jpg
These are but a few of dozens of traces recorded by
myself where we looked at drop-out-delay, contact
transition velocity, and contact bounce vs. various coil
suppression techniques (including simple placement
of a 120 ohm resistor across the coil!).
< BR> Bottom line is that anything you want to do will be fine . . . make it easy on yourself and be wary
of pronouncements and dire warnings from folk who
not been there nor done that. Do a failure mode
effects analysis and craft architectures that offer
a Plan-B for ALL uncomfortable failures. The road
to comfortable termination of flight is not paved with
prophylactics AGAINST failure . . . rather a PLAN for
dealing comfortably with any failure.
Bob . . .
|
[quote][b]
| - The Matronics AeroElectric-List Email Forum - | | Use the List Feature Navigator to browse the many List utilities available such as the Email Subscriptions page, Archive Search & Download, 7-Day Browse, Chat, FAQ, Photoshare, and much more:
http://www.matronics.com/Navigator?AeroElectric-List |
|
|
|
Back to top |
|
 |
Colyn Case
Joined: 12 Oct 2009 Posts: 13 Location: Thetford Center
|
Posted: Mon Oct 12, 2009 10:00 am Post subject: Re: Diodes vs. Bi-Directional Zeners for Contactors |
|
|
Bob,
I agree with you about being prepared for any contactor to fail and not to be overly concerned about that. A failure that results in not being able to operate the contactor should not in itself be a hazard to flight.
However, a failure that results in smoke, although in other ways benign, is undesirable. I would be interested in what happens to the coil circuit as a function of the failure mode of the suppression device. If it fails open, so what, you lost some suppression. If it fails closed I think you get a dead short on the coil circuit, in other words the wire that goes to your starter key and to ground.
On my airplane, I don't have that circuit fused, reasoning that the coil itself is going to melt down before the wire does. but if you put a device in parallel with the coil and it shorts, then depending on the characteristics of the device you've got smoke in the cockpit.
So either you have to choose a device which you are pretty sure is going to fail open, or you need to fuse that circuit, right? (I don't see a fuse shown in the diagrams in the appendix).
Taking the devices:
resistor - likely fail open
diode - ?
zener diode - fail closed
snapjack - ?
thanks,
Colyn
| - The Matronics AeroElectric-List Email Forum - | | Use the List Feature Navigator to browse the many List utilities available such as the Email Subscriptions page, Archive Search & Download, 7-Day Browse, Chat, FAQ, Photoshare, and much more:
http://www.matronics.com/Navigator?AeroElectric-List |
|
_________________ Colyn Case
colyncase@earthlink.net |
|
Back to top |
|
 |
Eric M. Jones
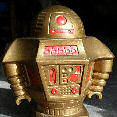
Joined: 10 Jan 2006 Posts: 565 Location: Massachusetts
|
Posted: Tue Oct 13, 2009 5:56 am Post subject: Re: Diodes vs. Bi-Directional Zeners for Contactors |
|
|
Bob N., you are truly to be admired for the limitless energy you have put into this subject. I don't know how you do it.
I sell "SnapJacks" bi-directional zeners for putting across the coils of relays, inductors, and especially contactors--as recommended by Tyco, Potter and Brumfield, Megavac, Kilovac, and virtually all other relay engineers who have ever looked at the problem.
But hey, you could be right! One lone voice in the wilderness. I admire you.
"Every act of conscious learning requires the willingness to suffer an injury to one's self-esteem...."
-Thomas Szasz
| - The Matronics AeroElectric-List Email Forum - | | Use the List Feature Navigator to browse the many List utilities available such as the Email Subscriptions page, Archive Search & Download, 7-Day Browse, Chat, FAQ, Photoshare, and much more:
http://www.matronics.com/Navigator?AeroElectric-List |
|
_________________ Eric M. Jones
www.PerihelionDesign.com
113 Brentwood Drive
Southbridge, MA 01550
(508) 764-2072
emjones(at)charter.net |
|
Back to top |
|
 |
user9253
Joined: 28 Mar 2008 Posts: 1908 Location: Riley TWP Michigan
|
Posted: Tue Oct 13, 2009 8:58 am Post subject: Re: Diodes vs. Bi-Directional Zeners for Contactors |
|
|
TYCO's document at Code: | http://relays.tycoelectronics.com/appnotes/app_pdfs/13c3311.pdf |
says, "It is the velocity of the armature that is most affected by coil suppression. If the suppressor provides a conducting path, thus allowing the stored energy in the relay's magnetic circuit to decay slowly, the armature motion will be retarded and the armature may even temporarily reverse direction."
TYCO's document seemed credible until the above paragraph. How can a relay start to drop out, then reverse direction? Where does the power come from to do this? Using a diode for arc suppression, the relay will start to drop out when the voltage decays to some point less than 12 volts. In order for the relay to reverse direction, the voltage will have to increase. But how could it increase? The voltage has already decayed to the point where the relay drops out, and the diode is still shorting out what little energy is left. It is common knowledge that a relay requires a higher voltage to pull in than to drop out. TYCO is suggesting the impossible. Making that ridiculous statement makes one question the validity of the whole document. The table showing the drop out times of various suppression devices does not make it clear exactly what time interval was measured. Was it the interval from when power to the coil was first shut off to the time that the contacts were fully opened? If so, that time is irrelevant to arcing of the relay contacts. The only time interval of concern is from when the relay contacts first start to open until they are open far enough to quench the arc. The important thing is, how much longer do relay contacts arc when using diode compared to using a zener? And is that time difference significant in our application?
I agree with Bob. The TYCO article is BS.
Mike Easley and Colyn Case are concerned about the arc-suppression diode shorting out across the main contactor. A 22awg wire can be used from the contactor fat terminal to the coil terminal, then a 18awg from the other side of the coil into the cockpit. In case of an unlikely short, the 22awg wire will burn open first, keeping smoke on the engine side of the firewall.
Joe
| - The Matronics AeroElectric-List Email Forum - | | Use the List Feature Navigator to browse the many List utilities available such as the Email Subscriptions page, Archive Search & Download, 7-Day Browse, Chat, FAQ, Photoshare, and much more:
http://www.matronics.com/Navigator?AeroElectric-List |
|
_________________ Joe Gores |
|
Back to top |
|
 |
nuckolls.bob(at)aeroelect Guest
|
Posted: Tue Oct 13, 2009 10:42 am Post subject: Diodes vs. Bi-Directional Zeners for Contactors |
|
|
I'm interested in comments on the relative merits of using diodes vs.
bi-directional zeners. Also, the failure modes of both devices. And
how to size the bi-directional zeners to minimize the chance of a
failure, especially a short failure.
What would happen if either were fail shorted due to high voltage?
Excellent question . . . and the answer goes directly
to countless studies and adjustment of design goals
for the purpose of producing an ACCEPTABLE reliability
factor (generally stated in failures per flight hour).
Any time we can deduce that the failure rate is better
than 1 in 10 to the minus 6 failures per flight hour
(i.e. 1,000,000 flight hours per failure), the guys
who worry about such things relax a lot.
Now, does such a determination say that all components
under study will last 1,000,000 hours? No, the
testing and calculations tell us that the AVERAGE
failure rate for a large population of identical
components is 1,000,000 hours per failure or better.
If you have a device fail in 500,000 hours, then
other components of that population will have to
do better than 1,000,000 hours for the average to
hold.
Experience shows us that robust and otherwise new
components which fall victim to errors of manufacturing
process will fail early (infant mortality) . . . especially
if operated at or just above extreme stress ratings
for that device. This process is called "screening"
and is the basis for Mil-Std-883 qualified components
favored in critical military and space programs. The
screening process is designed to precipitate infant
mortality failures.
Even then, some folks paid to worry will sandbag their
design goals by telling suppliers to DE-RATE their
already screened 883 components by some factor. Resistors
will be de-rated to 1/2 power. Capacitors operated at
1/2 rated voltage, etc. etc.
I've smiled when reading the purchase specs driven
by such worries. Virtually every product failure
over which I was given direction turned out to be
an error in design or process, not a failure of component
to meet requirements for which it was properly designed
and qualified. It seems like the guy turning the wrenches
is still the riskiest ingredient in the recipe. So let's
potential for stress induced failure of a diode across the
coil of a contactor. See:
http://www.fairchildsemi.com/ds/1N/1N4001.pdf
For the most part, we're building 14v airplanes with
a sprinkling of 28v. Okay, a 50v rated diode will have
a 2x headroom in a 28v airplane, 3.5x in a 14v airplane.
For a few cents more, one COULD install a 600V rated diode.
Man, talk about de-rating!
On the conduction side of the study, the typical 1A
diode (1N400x series) is designed and qualified to
conduct 1A at a max voltage drop of 1.1 volts. Okay,
this is 1.1 watts of heat being dumped out in that
diminutive glass or plastic package. Now, we never
SEE that 1.1 volts under our anticipated usage.
But let's take worst case.
CAPACITORS charge to some voltage will deliver that
SAME voltage at potentially HIGH current during
the discharge cycle. INDUCTORS charged to some current
will deliver that SAME current at potentially HIGH
voltage during their discharge cycle.
Now, here's an el-cheeso battery contactor running
coil current of .6 to 1.0 amps. When the circuit
is broken, we can expect a PULSE of current at no
more than 1.0 amps. Further, the duration of that
current is on the order of 200 milliseconds ramping
down from 1.0 amps to zero. Let's assume an AVERAGE
of 0.5 Amps over 200 milliseconds with a maximum
voltage drop of 1.1 volts. Hmmm . . . that's a worst
case value of 110 milljoules of energy over 0.2 seconds
dumped into a device DESIGNED to dissipate 1100 millijoules
of energy every second for an indefinite period of time.
May I suggest that this too is an exceedingly conservative
de-rating philosophy?
So while we're discussing potential failure modes
for becoming either shorted or open, let us not loose
our grip on probability of failure based on the expected
stresses versus stresses defined by the device's
design. Devices used for coil spike suppression are
VERY lightly taxed and therefore exceedingly low
failure rates.
Short answer is that "sizing" of these components
based on their electrical characteristics is a
exercise in no-value-added-worrying. I prefer to
size them for mechanical robustness as illustrated
many places in my writing and illustrating. The
beefier 1N5400 series devices are less likely to
be damaged by over-enthusiastic wrench turning.
Whether you use zeners-diode combos, bi-directional
Transorbs, resistors, diodes, etc will have no
observable effect on system reliability based on
ratings. But beating the little guys up with
wrench or hammer is another matter. The more
valid worry is not WHAT you use but HOW you
use it.
Bob . . .
---------------------------------------
( . . . a long habit of not thinking )
( a thing wrong, gives it a superficial )
( appearance of being right . . . )
( )
( -Thomas Paine 1776- )
---------------------------------------
| - The Matronics AeroElectric-List Email Forum - | | Use the List Feature Navigator to browse the many List utilities available such as the Email Subscriptions page, Archive Search & Download, 7-Day Browse, Chat, FAQ, Photoshare, and much more:
http://www.matronics.com/Navigator?AeroElectric-List |
|
|
|
Back to top |
|
 |
|
|
You cannot post new topics in this forum You cannot reply to topics in this forum You cannot edit your posts in this forum You cannot delete your posts in this forum You cannot vote in polls in this forum You cannot attach files in this forum You can download files in this forum
|
Powered by phpBB © 2001, 2005 phpBB Group
|