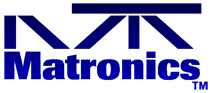 |
Matronics Email Lists Web Forum Interface to the Matronics Email Lists
|
View previous topic :: View next topic |
Author |
Message |
ribrdb(at)gmail.com Guest
|
Posted: Mon Aug 10, 2015 1:57 pm Post subject: electrical system planning |
|
|
I'm working on figuring out the system architecture for my plane.It's an rv9 with all glass panel and an O320 with electrically dependent fuel injection (EFII).
The mission is typically cross countries including some night flight and IFR, though it would typically be going through a layer of clouds to VFR on top.
Here's what I've got for my load analysis:
Fuel pump: 5 A
Ignition/Fuel injectors: 5 A
So already the SD-8 is out.
For minimal comfortable flight I'd add:
Primary EFIS: 3.1 A
Transponder: 0.4 A
Total: 13.5
Add in the rest of the avionics for normal flight:
gtn650 nav/com 2.2A
intercom 0.1A
adsb in 0.2A
Backup efis 3.1 A
(total 19.1)
Then 10A for pitot heat, and lights:
strobes 2.5A
position lights 1.2A
landing lights 1.8A
I'm not including the motors for trim, flaps, or auto pilot here. Also I'm assuming the comms aren't transmitting. Are these the right assumptions for the load analysis?
It seems like Z-12 is the best option for me here. I have to use a 20-30 amp backup alternator to keep the engine running. That gives me enough juice to keep nearly everything running, so Z-13/8 doesn't seem useful.
Z-12 shows an SD-20 backup alternator with it's own switch. I'm assuming normal operation is with Master on ALT and Aux Alternator on OFF. When you get low volts warning, you switch Master to BAT and Aux Alternator to ON.
Is there some advantage to wiring it this way instead of having the standby alternator take over automatically when the voltage drops? Or is that actually what Z-12 is showing, and you'd normally fly with Aux Alternator ON?
Also I see that Z-12 shows Battery, Master, and Endurance busses. What's the point? It seems I'd put the minimum equipment on the battery bus, and everything else could be on master. It's probably just as many switch flips to shed load on the master bus as it is to reconfigure the endurance bus.
I guess the endurance bus also give you an extra route to the battery if the master switch or battery contactor fails, but why not just put the important devices on the battery bus?
[quote][b]
| - The Matronics AeroElectric-List Email Forum - | | Use the List Feature Navigator to browse the many List utilities available such as the Email Subscriptions page, Archive Search & Download, 7-Day Browse, Chat, FAQ, Photoshare, and much more:
http://www.matronics.com/Navigator?AeroElectric-List |
|
|
|
Back to top |
|
 |
jmjones2000(at)mindspring Guest
|
Posted: Tue Aug 11, 2015 5:26 pm Post subject: electrical system planning |
|
|
Ryan,
I have a very similar setup using the efii system and used the Z13/8 diagram (modified for the efii components). I am very happy with it and would be glad to share my diagram with you if you'd like. I used a standard aircraft primary alternator and used the B&C 410H on the vacuum pump as my backup.
Keep in mind that it is unlikely that all of your electrical components will run continuously all the time. Also, you can manually load shed during operations that require the use of your backup alternator if needed. The 410H is a hefty alternator and will put plenty of amps to keep up with your system.
A low voltage warning system is absolutely critical!
Justin
On Aug 10, 2015, at 17:55, Ryan Brown <ribrdb(at)gmail.com (ribrdb(at)gmail.com)> wrote:
[quote]I'm working on figuring out the system architecture for my plane.It's an rv9 with all glass panel and an O320 with electrically dependent fuel injection (EFII).
The mission is typically cross countries including some night flight and IFR, though it would typically be going through a layer of clouds to VFR on top.
Here's what I've got for my load analysis:
Fuel pump: 5 A
Ignition/Fuel injectors: 5 A
So already the SD-8 is out.
For minimal comfortable flight I'd add:
Primary EFIS: 3.1 A
Transponder: 0.4 A
Total: 13.5
Add in the rest of the avionics for normal flight:
gtn650 nav/com 2.2A
intercom 0.1A
adsb in 0.2A
Backup efis 3.1 A
(total 19.1)
Then 10A for pitot heat, and lights:
strobes 2.5A
position lights 1.2A
landing lights 1.8A
I'm not including the motors for trim, flaps, or auto pilot here. Also I'm assuming the comms aren't transmitting. Are these the right assumptions for the load analysis?
It seems like Z-12 is the best option for me here. I have to use a 20-30 amp backup alternator to keep the engine running. That gives me enough juice to keep nearly everything running, so Z-13/8 doesn't seem useful.
Z-12 shows an SD-20 backup alternator with it's own switch. I'm assuming normal operation is with Master on ALT and Aux Alternator on OFF. When you get low volts warning, you switch Master to BAT and Aux Alternator to ON.
Is there some advantage to wiring it this way instead of having the standby alternator take over automatically when the voltage drops? Or is that actually what Z-12 is showing, and you'd normally fly with Aux Alternator ON?
Also I see that Z-12 shows Battery, Master, and Endurance busses. What's the point? It seems I'd put the minimum equipment on the battery bus, and everything else could be on master. It's probably just as many switch flips to shed load on the master bus as it is to reconfigure the endurance bus.
I guess the endurance bus also give you an extra route to the battery if the master switch or battery contactor fails, but why not just put the important devices on the battery bus?
Quote: |
D=3D=3D=3D=3D=3D=3D=3D=3D=3D=3D=3D=3D=3D=3D=3D=3D=3D=3D=3D=3D=3D=3D=3D=3D=3D=3D=3D=3D=3D=3D=3D=3D=3D=3D=3D=3D=3D=3D=3D=3D=3D=3D=3D=3D=3D
lectric-List"">http://www.matronics.com/Navigator?AeroElectric-List
D=3D=3D=3D=3D=3D=3D=3D=3D=3D=3D=3D=3D=3D=3D=3D=3D=3D=3D=3D=3D=3D=3D=3D=3D=3D=3D=3D=3D=3D=3D=3D=3D=3D=3D=3D=3D=3D=3D=3D=3D=3D=3D=3D=3D=3D
//forums.matronics.com
D=3D=3D=3D=3D=3D=3D=3D=3D=3D=3D=3D=3D=3D=3D=3D=3D=3D=3D=3D=3D=3D=3D=3D=3D=3D=3D=3D=3D=3D=3D=3D=3D=3D=3D=3D=3D=3D=3D=3D=3D=3D=3D=3D=3D=3D
ot;">http://www.matronics.com/contribution
D=3D=3D=3D=3D=3D=3D=3D=3D=3D=3D=3D=3D=3D=3D=3D=3D=3D=3D=3D=3D=3D=3D=3D=3D=3D=3D=3D=3D=3D=3D=3D=3D=3D=3D=3D=3D=3D=3D=3D=3D=3D=3D=3D=3D=3D
|
[b]
| - The Matronics AeroElectric-List Email Forum - | | Use the List Feature Navigator to browse the many List utilities available such as the Email Subscriptions page, Archive Search & Download, 7-Day Browse, Chat, FAQ, Photoshare, and much more:
http://www.matronics.com/Navigator?AeroElectric-List |
|
|
|
Back to top |
|
 |
nuckolls.bob(at)aeroelect Guest
|
Posted: Sun Aug 16, 2015 8:46 am Post subject: electrical system planning |
|
|
At 04:55 PM 8/10/2015, you wrote:
Quote: | I'm working on figuring out the system architecture for my plane. |
THE VERY FIRST TASK in crafting the elegant solution
for architecture in a projet like yours is to download
this form:
http://tinyurl.com/7jqypwj
and develop a load-picture for the various
phases of flight.
Do one page for each bus. Electrically dependent
engine stuff on battery bus, plan-b loads on
and E-bus, everything else on the main bus.
THEN . . . set design goals for endurance under
an alternator out condition and either
size a WELL MAINTAINED battery to meet that
goal or craft some combination of battery and
second alternator to meet the goal.
Then let's talk about the architecture that's
most friendly to meeting your design goals.
Are those 5A figures REAL, MEASURED current
values? Breaker sizes from a wiring diagram
are never indicative of ENERGY required to
operate the system.
This is a study the economics of energy
management to achieve operational goals
that determine whether a failure is
an emergency or a ho-hum event.
Bob . . . [quote][b]
| - The Matronics AeroElectric-List Email Forum - | | Use the List Feature Navigator to browse the many List utilities available such as the Email Subscriptions page, Archive Search & Download, 7-Day Browse, Chat, FAQ, Photoshare, and much more:
http://www.matronics.com/Navigator?AeroElectric-List |
|
|
|
Back to top |
|
 |
ribrdb(at)gmail.com Guest
|
Posted: Sun Aug 16, 2015 8:31 pm Post subject: electrical system planning |
|
|
Thanks Bob.The 5A figures are the estimates I got from the manufacturer for average consumption. I haven't measured it myself. The breaker size is 10A.
I filled out a spreadsheet with the load analysis for each stage here: https://goo.gl/0FPFIQ
I'm not entirely sure I have everything assigned to the right bus.
I estimate the plane will hold 5.5 hours of fuel, so I guess that's what my endurance goal should be.
That's over 70 amp hours just to keep the engine running, so it seems a backup alternator is a better bet than batteries.
One question I have is if my endurance goal should be 5.5 hours with pitot heat on. I don't plan on tons of ifr flight, and I kind of doubt my brain could handle 5 hours of instrument flight. So it seems like lower endurance for ifr cruise could be acceptable.
If I do want to keep the heater on with the backup alternator I need a little more than 20 amps. I'm a little confused looking at the alternators here. The SD-20 is described as a 20/30A alternator. What does that mean. I saw some mention that the vacuum pad on a continental spins faster, does that mean it's 30A on a continental and 20A on a lycoming?
The plane power FS14 is just listed as 30A, so I assume it can actually put out 30A on a lycoming.
On Sun, Aug 16, 2015 at 9:50 AM Robert L. Nuckolls, III <nuckolls.bob(at)aeroelectric.com (nuckolls.bob(at)aeroelectric.com)> wrote:
[quote] At 04:55 PM 8/10/2015, you wrote:
Quote: | I'm working on figuring out the system architecture for my plane. |
THE VERY FIRST TASK in crafting the elegant solution
for architecture in a projet like yours is to download
this form:
http://tinyurl.com/7jqypwj
and develop a load-picture for the various
phases of flight.
Do one page for each bus. Electrically dependent
engine stuff on battery bus, plan-b loads on
and E-bus, everything else on the main bus.
THEN . . . set design goals for endurance under
an alternator out condition and either
size a WELL MAINTAINED battery to meet that
goal or craft some combination of battery and
second alternator to meet the goal.
Then let's talk about the architecture that's
most friendly to meeting your design goals.
Are those 5A figures REAL, MEASURED current
values? Breaker sizes from a wiring diagram
are never indicative of ENERGY required to
operate the system.
This is a study the economics of energy
management to achieve operational goals
that determine whether a failure is
an emergency or a ho-hum event.
Bob . . .
Quote: |
ist" target="_blank">http://www.matronics.com/Navigator?AeroElectric-List
tp://forums.matronics.com
_blank">http://www.matronics.com/contribution
|
[b]
| - The Matronics AeroElectric-List Email Forum - | | Use the List Feature Navigator to browse the many List utilities available such as the Email Subscriptions page, Archive Search & Download, 7-Day Browse, Chat, FAQ, Photoshare, and much more:
http://www.matronics.com/Navigator?AeroElectric-List |
|
|
|
Back to top |
|
 |
nuckolls.bob(at)aeroelect Guest
|
Posted: Mon Aug 17, 2015 6:36 am Post subject: electrical system planning |
|
|
A t 11:29 PM 8/16/2015, you wrote:
Quote: | Thanks Bob.
The 5A figures are the estimates I got from the manufacturer for average consumption. I haven't measured it myself. The breaker size is 10A. |
When you get this airplane flying, I'd REALLY
like to get some data off it that describes
ENERGY measurements . . . but 5A probably
works for now.
Quote: | I filled out a spreadsheet with the load analysis for each stage here: https://goo.gl/0FPFIQ
I'm not entirely sure I have everything assigned to the right bus.
I estimate the plane will hold 5.5 hours of fuel, so I guess that's what my endurance goal should be. |
No guessing here . . . that's a number YOU pick
based on how you intend to use the airplane. If
you plan on frequent departures from airports
often clagged in and surrounded by mountains, then
the idea of endurance to carry you to demonstrably
lower-risk haven is a part of solid reasoning. But
if that comfortable termination of flight is
never more than say 2 hours away, then designing
and maintained that level of endurance is not
unreasonable.
The main thing is to know what the endurance numbers
are, preventative maintenance to insure those
numbers and risks go down markedly.
Quote: | That's over 70 amp hours just to keep the engine running, so it seems a backup alternator is a better bet than batteries. |
Bingo!
A second engine driven power source is ALWAYS the
best cost-weight-performance alternative to ANY
chemical system.
Quote: | One question I have is if my endurance goal should be 5.5 hours with pitot heat on. I don't plan on tons of ifr flight, and I kind of doubt my brain could handle 5 hours of instrument flight. So it seems like lower endurance for ifr cruise could be acceptable. |
Probably so . . .
Quote: |
If I do want to keep the heater on with the backup alternator I need a little more than 20 amps. I'm a little confused looking at the alternators here. The SD-20 is described as a 20/30A alternator. What does that mean. I saw some mention that the vacuum pad on a continental spins faster, does that mean it's 30A on a continental and 20A on a lycoming? |
I am not sure of the details . . . I've not had occasion
to touch the phycics of that product in about 20
years but I do understand that under presently
demonstrated conditions, its output can be that
high.
Quote: | The plane power FS14 is just listed as 30A, so I assume it can actually put out 30A on a lycoming. |
Pitot heat was never a really good idea on light
aircraft . . . yeah, it MAY have saved the bacon
for a hand-full of pilots in years gone by but
far more airplanes belabored with ice have gone down
in spite of knowing exactly what their airspeed
was before they hit the rocks.
Having 'little chippers' to deal with some forms
of ice (heated windshield patches, boots, pitot
heat) have offered too many pilots a false sense
of capability to deal with mother nature's vagaries.
Modern weather observation and prediction systems
are so capable that go-no go decision to launch
is far wiser than any notion of being able to 'deal
with a little ice' . . . same thing with those
little yellow, orange and red areas on the radar . . .
good reasons to just stay on the ground or take
another route.
My preference for conducting the FMEA says
keeping the tube warm is at the bottom of the
list with respect to other appliances on board.
Just for grins, noodle through the plan-c for dealing
with loss of airspeed indication. What do you KNOW
about handling qualities, changes of trim and
power that speak to impending stall? If that
airspeed value becomes suspect for what you believe
is high-probability of ice, I'll suggest that
plans to seek warmer environs far outweighs
any value of knowing exactly what your airspeed
unless you think that climbing is the path to
salvation . . . which is very seldom the case.
IAS as a warning for impending stall is
based on a CLEAN wing. I got a really big
lesson in fouled aerodynamics when a landing
in Hutchinson KS ended with the airplane plopping
down hard in the flare while yours truly was
patting himself on the butt for having kept
the needles centered for over fifteen minutes
in the clouds, outbound through procedure turns
and then all the way back to the threshold.
My instructor was grinning ear to ear and said,
"Okay Nuckolls . . . while you were glued to the
glass, your wings were taking on new shapes with
unpredictable performance. None of that C-172-
full-stall-flare stuff in instrument conditions.
Fly it like a Grumman . . . carrier landings are
called for unless you are CERTAIN that your wings
are golden."
You need to make up your own mind but it seems
to me that a Z-12 system with a 15 a.h. SVLA
battery would provide a comfortable reduction
in risks . . . especially if you consider pitot
heat to be more cosmetic than practical.
Bob . . . [quote][b]
| - The Matronics AeroElectric-List Email Forum - | | Use the List Feature Navigator to browse the many List utilities available such as the Email Subscriptions page, Archive Search & Download, 7-Day Browse, Chat, FAQ, Photoshare, and much more:
http://www.matronics.com/Navigator?AeroElectric-List |
|
|
|
Back to top |
|
 |
ribrdb(at)gmail.com Guest
|
Posted: Tue Aug 18, 2015 8:14 am Post subject: electrical system planning |
|
|
Thanks. I agree pitot heat does seem optional for the type of flying I plan on doing. I'd much rather just stay away from ice than try to fly through it.
So Z12 is what I was leaning towards. But I wonder what's the purpose of having the endurance bus if I have a 20 amp standby alternator? In alternator out conditions I can just keep the master on, and run just about anything I want. Why not just have an alternate feed switch for the master bus in case the master switch or battery contactor fails? On Aug 17, 2015 7:41 AM, "Robert L. Nuckolls, III" <nuckolls.bob(at)aeroelectric.com (nuckolls.bob(at)aeroelectric.com)> wrote:[quote] A t 11:29 PM 8/16/2015, you wrote:
Quote: | Thanks Bob.
The 5A figures are the estimates I got from the manufacturer for average consumption. I haven't measured it myself. The breaker size is 10A. |
When you get this airplane flying, I'd REALLY
like to get some data off it that describes
ENERGY measurements . . . but 5A probably
works for now.
Quote: | I filled out a spreadsheet with the load analysis for each stage here:Â https://goo.gl/0FPFIQ
I'm not entirely sure I have everything assigned to the right bus.
I estimate the plane will hold 5.5 hours of fuel, so I guess that's what my endurance goal should be. |
No guessing here . . . that's a number YOU pick
based on how you intend to use the airplane. If
you plan on frequent departures from airports
often clagged in and surrounded by mountains, then
the idea of endurance to carry you to demonstrably
lower-risk haven is a part of solid reasoning. But
if that comfortable termination of flight is
never more than say 2 hours away, then designing
and maintained that level of endurance is not
unreasonable.
The main thing is to know what the endurance numbers
are, preventative maintenance to insure those
numbers and risks go down markedly.
Quote: | That's over 70 amp hours just to keep the engine running, so it seems a backup alternator is a better bet than batteries. |
Bingo!
A second engine driven power source is ALWAYS the
best cost-weight-performance alternative to ANY
chemical system.
Quote: | One question I have is if my endurance goal should be 5.5 hours with pitot heat on. I don't plan on tons of ifr flight, and I kind of doubt my brain could handle 5 hours of instrument flight. So it seems like lower endurance for ifr cruise could be acceptable. |
Probably so . . .
Quote: |
If I do want to keep the heater on with the backup alternator I need a little more than 20 amps. I'm a little confused looking at the alternators here. The SD-20 is described as a 20/30A alternator. What does that mean. I saw some mention that the vacuum pad on a continental spins faster, does that mean it's 30A on a continental and 20A on a lycoming? |
I am not sure of the details . . . I've not had occasion
to touch the phycics of that product in about 20
years but I do understand that under presently
demonstrated conditions, its output can be that
high.
Quote: | The plane power FS14 is just listed as 30A, so I assume it can actually put out 30A on a lycoming. |
Pitot heat was never a really good idea on light
aircraft . . . yeah, it MAY have saved the bacon
for a hand-full of pilots in years gone by but
far more airplanes belabored with ice have gone down
in spite of knowing exactly what their airspeed
was before they hit the rocks.
Having 'little chippers' to deal with some forms
of ice (heated windshield patches, boots, pitot
heat) have offered too many pilots a false sense
of capability to deal with mother nature's vagaries.
Modern weather observation and prediction systems
are so capable that go-no go decision to launch
is far wiser than any notion of being able to 'deal
with a little ice' . . . same thing with those
little yellow, orange and red areas on the radar . . .
good reasons to just stay on the ground or take
another route.
My preference for conducting the FMEA says
keeping the tube warm is at the bottom of the
list with respect to other appliances on board.
Just for grins, noodle through the plan-c for dealing
with loss of airspeed indication. What do you KNOW
about handling qualities, changes of trim and
power that speak to impending stall? If that
airspeed value becomes suspect for what you believe
is high-probability of ice, I'll suggest that
plans to seek warmer environs far outweighs
any value of knowing exactly what your airspeed
unless you think that climbing is the path to
salvation . . . which is very seldom the case.
IAS as a warning for impending stall is
based on a CLEAN wing. I got a really big
lesson in fouled aerodynamics when a landing
in Hutchinson KS ended with the airplane plopping
down hard in the flare while yours truly was
patting himself on the butt for having kept
the needles centered for over fifteen minutes
in the clouds, outbound through procedure turns
and then all the way back to the threshold.
My instructor was grinning ear to ear and said,
"Okay Nuckolls . . . while you were glued to the
glass, your wings were taking on new shapes with
unpredictable performance. None of that C-172-
full-stall-flare stuff in instrument conditions.
Fly it like a Grumman . . . carrier landings are
called for unless you are CERTAIN that your wings
are golden."
You need to make up your own mind but it seems
to me that a Z-12 system with a 15 a.h. SVLA
battery would provide a comfortable reduction
in risks . . . especially if you consider pitot
heat to be more cosmetic than practical.
Bob . . . Quote: |
ist" target="_blank">http://www.matronics.com/Navigator?AeroElectric-List
tp://forums.matronics.com
_blank">http://www.matronics.com/contribution
|
[b]
| - The Matronics AeroElectric-List Email Forum - | | Use the List Feature Navigator to browse the many List utilities available such as the Email Subscriptions page, Archive Search & Download, 7-Day Browse, Chat, FAQ, Photoshare, and much more:
http://www.matronics.com/Navigator?AeroElectric-List |
|
|
|
Back to top |
|
 |
user9253
Joined: 28 Mar 2008 Posts: 1908 Location: Riley TWP Michigan
|
Posted: Tue Aug 18, 2015 9:05 am Post subject: Re: electrical system planning |
|
|
Quote: | Why not just have an alternate feed switch for the master bus in case the master switch or battery contactor fails? |
Use a DPDT switch wired so that when the alternate feed is turned on, the starter circuit will be disabled. Not having that feature will risk burning up the alternate feed switch while starting the engine with the master contactor inadvertently shut off.
Joe
| - The Matronics AeroElectric-List Email Forum - | | Use the List Feature Navigator to browse the many List utilities available such as the Email Subscriptions page, Archive Search & Download, 7-Day Browse, Chat, FAQ, Photoshare, and much more:
http://www.matronics.com/Navigator?AeroElectric-List |
|
_________________ Joe Gores |
|
Back to top |
|
 |
nuckolls.bob(at)aeroelect Guest
|
Posted: Tue Aug 18, 2015 2:32 pm Post subject: electrical system planning |
|
|
At 11:12 AM 8/18/2015, you wrote:
Quote: | Thanks. I agree pitot heat does seem optional for the type of flying I plan on doing. I'd much rather just stay away from ice than try to fly through it.
So Z12 is what I was leaning towards. But I wonder what's the purpose of having the endurance bus if I have a 20 amp standby alternator? In alternator out conditions I can just keep the master on, and run just about anything I want. Why not just have an alternate feed switch for the master bus in case the master switch or battery contactor fails? |
there are dozens of variations on a theme . . .
Z-12 is Z-11 with the addition of a standby
alternator that auto-switches when fitted with
the SB-1 regulator that does not give up
any of the risk management features of Z-11.
You may choose to have avionics busses and
associated master switches. Extra batteries,
or any number of variations. If you don't see
a need for the e-bus and want to leave it off,
by all means. If you have an alternative for
dealing with a contactor failure, that's okay
too.
Bob . . . [quote][b]
| - The Matronics AeroElectric-List Email Forum - | | Use the List Feature Navigator to browse the many List utilities available such as the Email Subscriptions page, Archive Search & Download, 7-Day Browse, Chat, FAQ, Photoshare, and much more:
http://www.matronics.com/Navigator?AeroElectric-List |
|
|
|
Back to top |
|
 |
jmjones2000(at)mindspring Guest
|
Posted: Tue Aug 18, 2015 4:13 pm Post subject: electrical system planning |
|
|
All of Bob's Z diagrams are phenomenal and do the job well. When deciding on the diagram to use, keep in mind the more batteries and more complexity, the more weight you will add to your small aircraft.
I'm sure anything you choose will suit you well and you will be happy about your decision.
I fly in remote Alaska and chose the Z13/8 (with a B&C 410H http://www.bandc.biz/alternator20ampshomebuilt1.aspx ) and am happy with it. The EFII system uses surprisingly small amperage when it's running, and when you wire the Z13/8 to the EFII system you have redundancy and reliability with 2 alternators and a battery. The 410h alternator provides plenty of amperage to run the full EFII system.
I wired my system, and set procedures with the ability to shut the master switch off, allowing the engine to continue to run (dual ECUs). I don't think I will ever have to do this, but it is nice to NOT have a master switch that will shut the engine off.
I also used milspec lever-lock switches for all of the EFII components to prohibit inadvertent actuation.
I am willing to share any pictures, part numbers, or drawings to anyone interested.
I would like to take this opportunity to thank Bob Nuckolls for his knowledge, patience, time, and willingness to help and teach us. Experimental aviation as a whole would not be as safe or the same without you.
Justin
On Aug 18, 2015, at 18:30, Robert L. Nuckolls, III <nuckolls.bob(at)aeroelectric.com (nuckolls.bob(at)aeroelectric.com)> wrote:
[quote] At 11:12 AM 8/18/2015, you wrote:
Quote: | Thanks. I agree pitot heat does seem optional for the type of flying I plan on doing. I'd much rather just stay away from ice than try to fly through it.
So Z12 is what I was leaning towards. But I wonder what's the purpose of having the endurance bus if I have a 20 amp standby alternator? In alternator out conditions I can just keep the master on, and run just about anything I want. Why not just have an alternate feed switch for the master bus in case the master switch or battery contactor fails? |
there are dozens of variations on a theme . . .
Z-12 is Z-11 with the addition of a standby
alternator that auto-switches when fitted with
the SB-1 regulator that does not give up
any of the risk management features of Z-11.
You may choose to have avionics busses and
associated master switches. Extra batteries,
or any number of variations. If you don't see
a need for the e-bus and want to leave it off,
by all means. If you have an alternative for
dealing with a contactor failure, that's okay
too.
Bob . . . Quote: |
===================================
st">http://www.matronics.com/Navigator?AeroElectric-List
===================================
cs.com
===================================
matronics.com/contribution
===================================
|
[b]
| - The Matronics AeroElectric-List Email Forum - | | Use the List Feature Navigator to browse the many List utilities available such as the Email Subscriptions page, Archive Search & Download, 7-Day Browse, Chat, FAQ, Photoshare, and much more:
http://www.matronics.com/Navigator?AeroElectric-List |
|
|
|
Back to top |
|
 |
wtmills
Joined: 05 Feb 2007 Posts: 32
|
Posted: Tue Aug 18, 2015 5:12 pm Post subject: electrical system planning |
|
|
Justin -
The complimentary finish is right on (as is the rest).
Thank you Bob -
Bill
SF bay area
AEC seminar KLVK (1998?)
Do not archive
Sent via the Samsung Galaxy Note® II, an AT&T 4G LTE smartphone
<div>-------- Original message --------</div><div>From: Justin Jones <jmjones2000(at)mindspring.com> </div><div>Date:08/18/2015 5:12 PM (GMT-08:00) </div><div>To: aeroelectric-list(at)matronics.com </div><div>Subject: Re: AeroElectric-List: electrical system planning </div><div>
</div>All of Bob's Z diagrams are phenomenal and do the job well. When deciding on the diagram to use, keep in mind the more batteries and more complexity, the more weight you will add to your small aircraft.
I'm sure anything you choose will suit you well and you will be happy about your decision.
I fly in remote Alaska and chose the Z13/8 (with a B&C 410H http://www.bandc.biz/alternator20ampshomebuilt1.aspx ) and am happy with it. The EFII system uses surprisingly small amperage when it's running, and when you wire the Z13/8 to the EFII system you have redundancy and reliability with 2 alternators and a battery. The 410h alternator provides plenty of amperage to run the full EFII system.
I wired my system, and set procedures with the ability to shut the master switch off, allowing the engine to continue to run (dual ECUs). I don't think I will ever have to do this, but it is nice to NOT have a master switch that will shut the engine off.
I also used milspec lever-lock switches for all of the EFII components to prohibit inadvertent actuation.
I am willing to share any pictures, part numbers, or drawings to anyone interested.
I would like to take this opportunity to thank Bob Nuckolls for his knowledge, patience, time, and willingness to help and teach us. Experimental aviation as a whole would not be as safe or the same without you.
Justin
On Aug 18, 2015, at 18:30, Robert L. Nuckolls, III <nuckolls.bob(at)aeroelectric.com> wrote:
At 11:12 AM 8/18/2015, you wrote:
Thanks. I agree pitot heat does seem optional for the type of flying I plan on doing. I'd much rather just stay away from ice than try to fly through it.
So Z12 is what I was leaning towards. But I wonder what's the purpose of having the endurance bus if I have a 20 amp standby alternator? In alternator out conditions I can just keep the master on, and run just about anything I want. Why not just have an alternate feed switch for the master bus in case the master switch or battery contactor fails?
there are dozens of variations on a theme . . .
Z-12 is Z-11 with the addition of a standby
alternator that auto-switches when fitted with
the SB-1 regulator that does not give up
any of the risk management features of Z-11.
You may choose to have avionics busses and
associated master switches. Extra batteries,
or any number of variations. If you don't see
a need for the e-bus and want to leave it off,
by all means. If you have an alternative for
dealing with a contactor failure, that's okay
too.
Bob . . .
===================================
st">http://www.matronics.com/Navigator?AeroElectric-List
===================================
cs.com
===================================
matronics.com/contribution
===================================
| - The Matronics AeroElectric-List Email Forum - | | Use the List Feature Navigator to browse the many List utilities available such as the Email Subscriptions page, Archive Search & Download, 7-Day Browse, Chat, FAQ, Photoshare, and much more:
http://www.matronics.com/Navigator?AeroElectric-List |
|
|
|
Back to top |
|
 |
Mauledriver(at)nc.rr.com Guest
|
Posted: Tue Aug 18, 2015 8:10 pm Post subject: electrical system planning |
|
|
Yes it is - Thanks Bob!
Bill "incl the Kitchen Sink" Watson
On 8/18/2015 9:11 PM, William Mills wrote:
[quote] Justin -
The complimentary finish is right on (as is the rest).
Thank you Bob -
Bill
SF bay area
AEC seminar KLVK (1998?)
Do not archive
Sent via the Samsung Galaxy Note® II, an AT&T 4G LTE smartphone
-------- Original message --------
From: Justin Jones
Date:08/18/2015 5:12 PM (GMT-08:00)
To: aeroelectric-list(at)matronics.com (aeroelectric-list(at)matronics.com)
Subject: Re: electrical system planning
All of Bob's Z diagrams are phenomenal and do the job well. When deciding on the diagram to use, keep in mind the more batteries and more complexity, the more weight you will add to your small aircraft.
I'm sure anything you choose will suit you well and you will be happy about your decision.
I fly in remote Alaska and chose the Z13/8 (with a B&C 410H http://www.bandc.biz/alternator20ampshomebuilt1.aspx ) and am happy with it. The EFII system uses surprisingly small amperage when it's running, and when you wire the Z13/8 to the EFII system you have redundancy and reliability with 2 alternators and a battery. The 410h alternator provides plenty of amperage to run the full EFII system.
I wired my system, and set procedures with the ability to shut the master switch off, allowing the engine to continue to run (dual ECUs). I don't think I will ever have to do this, but it is nice to NOT have a master switch that will shut the engine off.
I also used milspec lever-lock switches for all of the EFII components to prohibit inadvertent actuation.
I am willing to share any pictures, part numbers, or drawings to anyone interested.
I would like to take this opportunity to thank Bob Nuckolls for his knowledge, patience, time, and willingness to help and teach us. Experimental aviation as a whole would not be as safe or the same without you.
Justin
On Aug 18, 2015, at 18:30, Robert L. Nuckolls, III <nuckolls.bob(at)aeroelectric.com (nuckolls.bob(at)aeroelectric.com)> wrote:
Quote: | At 11:12 AM 8/18/2015, you wrote:
Quote: | Thanks. I agree pitot heat does seem optional for the type of flying I plan on doing. I'd much rather just stay away from ice than try to fly through it.
So Z12 is what I was leaning towards. But I wonder what's the purpose of having the endurance bus if I have a 20 amp standby alternator? In alternator out conditions I can just keep the master on, and run just about anything I want. Why not just have an alternate feed switch for the master bus in case the master switch or battery contactor fails? |
there are dozens of variations on a theme . . .
Z-12 is Z-11 with the addition of a standby
alternator that auto-switches when fitted with
the SB-1 regulator that does not give up
any of the risk management features of Z-11.
You may choose to have avionics busses and
associated master switches. Extra batteries,
or any number of variations. If you don't see
a need for the e-bus and want to leave it off,
by all means. If you have an alternative for
dealing with a contactor failure, that's okay
too.
Bob . . .
| ���~���,���%��4�M4}�r�����{(����8^��W����.+- f��Z+�e,z�^1�k�x�����W���ް֯����hn�0��azf�ȸ���b�+bz�.r�.+-Rҹ� �*m�����b��j�!�'����6��0��j�(at)(at)�h��!j���ٮr�r��桭���� 0��k�x���&�֯������%y�k����m����&j��',r��5�h���I^r��p�����4N4��X(at)E9I&�z �j�(�ק��l��ڊV����j�^Y�Ţ����ky�m���~��ɚ��'���hm���~��ɚ��'���o�.+- ���&�*'Y�Ҋד���ʋ����������.��+�ƭ�:ږW���(at)vh�j�~m���� ���'���oܢ{k��������0��k�x���&��'����ب���o�����ۡܿ�٥
No virus found in this message.
Checked by AVG - www.avg.com
Date: 08/18/15 [b]
| - The Matronics AeroElectric-List Email Forum - | | Use the List Feature Navigator to browse the many List utilities available such as the Email Subscriptions page, Archive Search & Download, 7-Day Browse, Chat, FAQ, Photoshare, and much more:
http://www.matronics.com/Navigator?AeroElectric-List |
|
|
|
Back to top |
|
 |
donvansanten(at)gmail.com Guest
|
Posted: Tue Aug 18, 2015 8:24 pm Post subject: electrical system planning |
|
|
The battery contactor pulls nearly a full amp. Also it is very easy to shed unneeded load by shutting the main down and going with the "E" bus. On Aug 18, 2015 9:20 AM, "Ryan Brown" <ribrdb(at)gmail.com (ribrdb(at)gmail.com)> wrote:[quote]
Thanks. I agree pitot heat does seem optional for the type of flying I plan on doing. I'd much rather just stay away from ice than try to fly through it.
So Z12 is what I was leaning towards. But I wonder what's the purpose of having the endurance bus if I have a 20 amp standby alternator? In alternator out conditions I can just keep the master on, and run just about anything I want. Why not just have an alternate feed switch for the master bus in case the master switch or battery contactor fails? On Aug 17, 2015 7:41 AM, "Robert L. Nuckolls, III" <nuckolls.bob(at)aeroelectric.com (nuckolls.bob(at)aeroelectric.com)> wrote: Quote: | A t 11:29 PM 8/16/2015, you wrote:
Quote: | Thanks Bob.
The 5A figures are the estimates I got from the manufacturer for average consumption. I haven't measured it myself. The breaker size is 10A. |
When you get this airplane flying, I'd REALLY
like to get some data off it that describes
ENERGY measurements . . . but 5A probably
works for now.
Quote: | I filled out a spreadsheet with the load analysis for each stage here:Â https://goo.gl/0FPFIQ
I'm not entirely sure I have everything assigned to the right bus.
I estimate the plane will hold 5.5 hours of fuel, so I guess that's what my endurance goal should be. |
No guessing here . . . that's a number YOU pick
based on how you intend to use the airplane. If
you plan on frequent departures from airports
often clagged in and surrounded by mountains, then
the idea of endurance to carry you to demonstrably
lower-risk haven is a part of solid reasoning. But
if that comfortable termination of flight is
never more than say 2 hours away, then designing
and maintained that level of endurance is not
unreasonable.
The main thing is to know what the endurance numbers
are, preventative maintenance to insure those
numbers and risks go down markedly.
Quote: | That's over 70 amp hours just to keep the engine running, so it seems a backup alternator is a better bet than batteries. |
Bingo!
A second engine driven power source is ALWAYS the
best cost-weight-performance alternative to ANY
chemical system.
Quote: | One question I have is if my endurance goal should be 5.5 hours with pitot heat on. I don't plan on tons of ifr flight, and I kind of doubt my brain could handle 5 hours of instrument flight. So it seems like lower endurance for ifr cruise could be acceptable. |
Probably so . . .
Quote: |
If I do want to keep the heater on with the backup alternator I need a little more than 20 amps. I'm a little confused looking at the alternators here. The SD-20 is described as a 20/30A alternator. What does that mean. I saw some mention that the vacuum pad on a continental spins faster, does that mean it's 30A on a continental and 20A on a lycoming? |
I am not sure of the details . . . I've not had occasion
to touch the phycics of that product in about 20
years but I do understand that under presently
demonstrated conditions, its output can be that
high.
Quote: | The plane power FS14 is just listed as 30A, so I assume it can actually put out 30A on a lycoming. |
Pitot heat was never a really good idea on light
aircraft . . . yeah, it MAY have saved the bacon
for a hand-full of pilots in years gone by but
far more airplanes belabored with ice have gone down
in spite of knowing exactly what their airspeed
was before they hit the rocks.
Having 'little chippers' to deal with some forms
of ice (heated windshield patches, boots, pitot
heat) have offered too many pilots a false sense
of capability to deal with mother nature's vagaries.
Modern weather observation and prediction systems
are so capable that go-no go decision to launch
is far wiser than any notion of being able to 'deal
with a little ice' . . . same thing with those
little yellow, orange and red areas on the radar . . .
good reasons to just stay on the ground or take
another route.
My preference for conducting the FMEA says
keeping the tube warm is at the bottom of the
list with respect to other appliances on board.
Just for grins, noodle through the plan-c for dealing
with loss of airspeed indication. What do you KNOW
about handling qualities, changes of trim and
power that speak to impending stall? If that
airspeed value becomes suspect for what you believe
is high-probability of ice, I'll suggest that
plans to seek warmer environs far outweighs
any value of knowing exactly what your airspeed
unless you think that climbing is the path to
salvation . . . which is very seldom the case.
IAS as a warning for impending stall is
based on a CLEAN wing. I got a really big
lesson in fouled aerodynamics when a landing
in Hutchinson KS ended with the airplane plopping
down hard in the flare while yours truly was
patting himself on the butt for having kept
the needles centered for over fifteen minutes
in the clouds, outbound through procedure turns
and then all the way back to the threshold.
My instructor was grinning ear to ear and said,
"Okay Nuckolls . . . while you were glued to the
glass, your wings were taking on new shapes with
unpredictable performance. None of that C-172-
full-stall-flare stuff in instrument conditions.
Fly it like a Grumman . . . carrier landings are
called for unless you are CERTAIN that your wings
are golden."
You need to make up your own mind but it seems
to me that a Z-12 system with a 15 a.h. SVLA
battery would provide a comfortable reduction
in risks . . . especially if you consider pitot
heat to be more cosmetic than practical.
Bob . . .
ist" target="_blank">http://www.matronics.com/Navigator?AeroElectric-List
tp://forums.matronics.com
_blank">http://www.matronics.com/contribution
| [b]
| - The Matronics AeroElectric-List Email Forum - | | Use the List Feature Navigator to browse the many List utilities available such as the Email Subscriptions page, Archive Search & Download, 7-Day Browse, Chat, FAQ, Photoshare, and much more:
http://www.matronics.com/Navigator?AeroElectric-List |
|
|
|
Back to top |
|
 |
nuckolls.bob(at)aeroelect Guest
|
Posted: Wed Aug 19, 2015 6:02 am Post subject: electrical system planning |
|
|
At 11:21 PM 8/18/2015, you wrote:
Quote: | The battery contactor pulls nearly a full amp. Also it is very easy to shed unneeded load by shutting the main down and going with the "E" bus. |
Z-12 doesn't give you the option of running
with the battery contactor open . . . Z13-8
DID offer that mode . . . due to the limited
output from the SD-8. Of course, it also offers
a calculated plan-c for operating battery
only.
I once offered a Z-13/20 utilizing the
SD-20 . . . kinda messy and I pulled it.
I might do some asphalt-cogitation on another
pass at it. In the mean time, Z-12 is
exemplary of architectures flying on hundreds
of TC aircraft of the production lines of
Beech, Mooney, Piper et. als. . . . except
their 'e-bus' is an (ugh!!) 'avionics-bus'.
Bob . . . [quote][b]
| - The Matronics AeroElectric-List Email Forum - | | Use the List Feature Navigator to browse the many List utilities available such as the Email Subscriptions page, Archive Search & Download, 7-Day Browse, Chat, FAQ, Photoshare, and much more:
http://www.matronics.com/Navigator?AeroElectric-List |
|
|
|
Back to top |
|
 |
ribrdb(at)gmail.com Guest
|
Posted: Wed Aug 19, 2015 10:00 am Post subject: electrical system planning |
|
|
I'm looking at Z-12 Rev M and it does show an E-Bus Alternate Feed switch. I'm trying to understand why it's there. I imagine two possible reasons:1) You could shut off the master switch to avoid the 1 amp contactor draw in main alternator out situtations
2) You could still run the e-bus if your master switch or contactor fails in flight. I don't know if that's the sort of failure that would happen in flight.
But I'm not sure if either, both, or neither of those are why it's included in the diagram.
On Wed, Aug 19, 2015 at 7:07 AM Robert L. Nuckolls, III <nuckolls.bob(at)aeroelectric.com (nuckolls.bob(at)aeroelectric.com)> wrote:
[quote] At 11:21 PM 8/18/2015, you wrote:
Quote: | The battery contactor pulls nearly a full amp. Also it is very easy to shed unneeded load by shutting the main down and going with the "E" bus. |
Z-12 doesn't give you the option of running
with the battery contactor open . . . Z13-8
DID offer that mode . . . due to the limited
output from the SD-8. Of course, it also offers
a calculated plan-c for operating battery
only.
I once offered a Z-13/20 utilizing the
SD-20 . . . kinda messy and I pulled it.
I might do some asphalt-cogitation on another
pass at it. In the mean time, Z-12 is
exemplary of architectures flying on hundreds
of TC aircraft of the production lines of
Beech, Mooney, Piper et. als. . . . except
their 'e-bus' is an (ugh!!) 'avionics-bus'.
Bob . . .
Quote: |
ist" target="_blank">http://www.matronics.com/Navigator?AeroElectric-List
tp://forums.matronics.com
_blank">http://www.matronics.com/contribution
|
[b]
| - The Matronics AeroElectric-List Email Forum - | | Use the List Feature Navigator to browse the many List utilities available such as the Email Subscriptions page, Archive Search & Download, 7-Day Browse, Chat, FAQ, Photoshare, and much more:
http://www.matronics.com/Navigator?AeroElectric-List |
|
|
|
Back to top |
|
 |
Jump4way
Joined: 18 May 2015 Posts: 14
|
Posted: Wed Aug 19, 2015 1:37 pm Post subject: Re: electrical system planning |
|
|
I'm planning a similar setup to what the original poster has mentioned. I too am trying to decide which Z diagram is better to follow. I have decided on a dual alternator and single battery setup.
I have calculated my EBUS at 13.5 amps and my Battery Bus at 3.5 amps. I don't feel the 8amp dynamo would put out quite the current to meet my need although I understand not everything on the list would be used continuously so actual usuage would be closer to the 8 amps, I just seem to feel more comfortable with a little more margin.
My question is if I were to use the 20amp alternator, or 30amp from planepower, which Z diagram would fit this better? The Z12M or Z13/8? Looking at the Z12, the alternator seems to tie in to the cold side of the battery master so if you want to load shed by shutting off the battery master, you will also shut off alternator power to the EBUS. Is the intent to never have to load shed with Z12 unless you were to suffer a rare dual alternator failure? I like the idea of the secondary alterator running in tandem with the primary alternator and picking up the load once bus voltage drops below 13.5 volts so the power transfer requires no user input.
I'm undecided on all of the avionics that I'm going to install at this point but I'm fairly confident that the total continuous load will not exceed 20amps so the need to load shed is not likely. Is it worth designing the system for possible future growth and the need to load shed? If that is the case, would there be any reason I could not tie the 20amp standby alternator controlled with the SB!B-14 on the hot side of the battery contactor to give me the option of powering the EBUS with the master switch off?
Are there any reliability considerations to take in to account that I'm not thinking of? Is the 8amp dynamo more reliable than the 20amp alternators or is it more of a weight and money thing?
Sorry if I derailed the original posters thread. I appreciate any feedback you all might have to offer.
| - The Matronics AeroElectric-List Email Forum - | | Use the List Feature Navigator to browse the many List utilities available such as the Email Subscriptions page, Archive Search & Download, 7-Day Browse, Chat, FAQ, Photoshare, and much more:
http://www.matronics.com/Navigator?AeroElectric-List |
|
|
|
Back to top |
|
 |
nuckolls.bob(at)aeroelect Guest
|
Posted: Wed Aug 19, 2015 6:46 pm Post subject: electrical system planning |
|
|
At 04:37 PM 8/19/2015, you wrote:
--> AeroElectric-List message posted by: "Jump4way" <andydelk(at)gmail.com>
I'm planning a similar setup to what the original poster has mentioned. I too am trying to decide which Z diagram is better to follow. I have decided on a dual alternator and single battery setup.
I have calculated my EBUS at 13.5 amps and my Battery Bus at 3.5 amps. I don't feel the 8amp dynamo would put out quite the current to meet my need although I understand not everything on the list would be used continuously so actual usuage would be closer to the 8 amps, I just seem to feel more comfortable with a little more margin.
"margin"????? With a 17A minimum running load
and an 8A standby alternator, you have NO margin.
My question is if I were to use the 20amp alternator, or 30amp from planepower, which Z diagram would fit this better? The Z12M or Z13/8?
Check with B&C . . . I think their larger spline
drive alternators are good for more than 20A.
Z-13/8 was NEVER intended to power an airplane with
a total running load greater than 8-10A and the
configuration was crafted to reduce running loads by
the 0.7A contactor coil . . . Z-13/8 is not an
option for you.
Looking at the Z12, the alternator seems to tie in to the cold side of the battery master so if you want to load shed by shutting off the battery master, you will also shut off alternator power to the EBUS. Is the intent to never have to load shed with Z12 unless you were to suffer a rare dual alternator failure?
Yes . . . That's what is done in hundreds . . .
perhaps over a thousand TC aircraft that run
a variant of Z-12.
I like the idea of the secondary alterator running in tandem with the primary alternator and picking up the load once bus voltage drops below 13.5 volts so the power transfer requires no user input.
I'm undecided on all of the avionics that I'm going to install at this point but I'm fairly confident that the total continuous load will not exceed 20amps so the need to load shed is not likely. Is it worth designing the system for possible future growth and the need to load shed?
Reducing loads is usually pretty easy . . . it's
call and OFF switch. The SB-1 regulator flashes
a light at you until you exploit a sufficient number
off OFF switches to reduce total load below 20A.
If that is the case, would there be any reason I could not tie the 20amp standby alternator controlled with the SB!B-14 on the hot side of the battery contactor to give me the option of powering the EBUS with the master switch off?
Are there any reliability considerations to take in to account that I'm not thinking of? Is the 8amp dynamo more reliable than the 20amp alternators or is it more of a weight and money thing?
Sorry if I derailed the original posters thread. I appreciate any feedback you all might have to offer.
Read the notes that go with the Z-figures. The whole
purpose of a standby alternator and e-bus is to maximize
conservation of energy in the EN ROUTE mode of flight.
How may electro-whizzies to you NEED to comfortably
achieve the descent/approach waypoint?
If you've turned a lot of stuff OFF . . . total loads
en route loads below 8A, then you have all
the battery's capacity in reserve for approach to
landing when you turn everything on that's useful for
comfortable termination of the flight.
This is what the load analysis sheets are all about
on the website. In the RARE instance that you DO
need to conserve power, have a check-list driven
plan-B to keep it from becoming an emergency. Odds
are, you don't need much hardware to get you to the
destination airport traffic area.
Z-13/8 is probably suited to 99% of all OBAM aircraft
flying if the owner/operator takes the time to
craft and implement a minimal power en-route mode
of energy consumption.
The airplanes I've rented didn't have standby alternators
or e-busses. Yet, loss of the alternator was not going to
have me looking for the asphalt 5 miles away. Here's
my "ebus" for TC aircraft.
http://tinyurl.com/ok7sjzt
I shut the whole electrical system down and leave it
off until time to enter the traffic area.
An e-bus running 13.5A is not an ENDURANCE BUS.
My suggestion to you is assume Z-13/8 and then see
if you can get total running loads below 8A . . .
actually 10A can probably be supported without seriously
discharging the battery.
Bob . . . [quote][b]
| - The Matronics AeroElectric-List Email Forum - | | Use the List Feature Navigator to browse the many List utilities available such as the Email Subscriptions page, Archive Search & Download, 7-Day Browse, Chat, FAQ, Photoshare, and much more:
http://www.matronics.com/Navigator?AeroElectric-List |
|
|
|
Back to top |
|
 |
jmjones2000(at)mindspring Guest
|
Posted: Wed Aug 19, 2015 7:56 pm Post subject: electrical system planning |
|
|
The Z13/8 with a B&C 410H vacuum-pad drive alternator (substituted for the SD8) is more than capable of running a Dual ECU EFII system indefinitely. The B&C 410H will power 13.5 amps without an issue, but I am guessing the actual draw would be less than 13.5 Amps. From what I have read here, it seems that most people overestimate the amperage that their “electric whizzies” actually draw. Some folks tend to use the peak draw as the number for each of the items. Often peak draw is not sustained for the entire operation and should therefore not be used as the continuous operation number. Best to measure each device’s amp draw prior to system planning and implementation.
With a primary alternator and a backup alternator that is capable of running the required loads, you have effectively reduced the chances of a negative outcome due to electrical system exhaustion by a very large margin (greatly reduced risk). The chances of a dual alternator failure is very slim. If you know the actual draw of your system (running on the Ebus), you can experience a dual alternator failure, have the right procedures in place, and still know the amount of time you have until your propeller will stop pulling you. (Dependent on your battery’s size and health)
Id rather have 2 alternators and a single battery than a single alternator and 2 batteries. An appropriately sized backup alternator will easily outlast 2 batteries, and is much lighter to boot.
Justin
Quote: | On Aug 19, 2015, at 6:44 PM, Robert L. Nuckolls, III <nuckolls.bob(at)aeroelectric.com (nuckolls.bob(at)aeroelectric.com)> wrote:
At 04:37 PM 8/19/2015, you wrote: --> AeroElectric-List message posted by: "Jump4way" <andydelk(at)gmail.com (andydelk(at)gmail.com)> I'm planning a similar setup to what the original poster has mentioned. I too am trying to decide which Z diagram is better to follow. I have decided on a dual alternator and single battery setup. I have calculated my EBUS at 13.5 amps and my Battery Bus at 3.5 amps. I don't feel the 8amp dynamo would put out quite the current to meet my need although I understand not everything on the list would be used continuously so actual usuage would be closer to the 8 amps, I just seem to feel more comfortable with a little more margin. "margin"????? With a 17A minimum running load and an 8A standby alternator, you have NO margin. My question is if I were to use the 20amp alternator, or 30amp from planepower, which Z diagram would fit this better? The Z12M or Z13/8? Check with B&C . . . I think their larger spline drive alternators are good for more than 20A. Z-13/8 was NEVER intended to power an airplane with a total running load greater than 8-10A and the configuration was crafted to reduce running loads by the 0.7A contactor coil . . . Z-13/8 is not an option for you. Looking at the Z12, the alternator seems to tie in to the cold side of the battery master so if you want to load shed by shutting off the battery master, you will also shut off alternator power to the EBUS. Is the intent to never have to load shed with Z12 unless you were to suffer a rare dual alternator failure? Yes . . . That's what is done in hundreds . . . perhaps over a thousand TC aircraft that run a variant of Z-12. I like the idea of the secondary alterator running in tandem with the primary alternator and picking up the load once bus voltage drops below 13.5 volts so the power transfer requires no user input. I'm undecided on all of the avionics that I'm going to install at this point but I'm fairly confident that the total continuous load will not exceed 20amps so the need to load shed is not likely. Is it worth designing the system for possible future growth and the need to load shed? Reducing loads is usually pretty easy . . . it's call and OFF switch. The SB-1 regulator flashes a light at you until you exploit a sufficient number off OFF switches to reduce total load below 20A. If that is the case, would there be any reason I could not tie the 20amp standby alternator controlled with the SB!B-14 on the hot side of the battery contactor to give me the option of powering the EBUS with the master switch off? Are there any reliability considerations to take in to account that I'm not thinking of? Is the 8amp dynamo more reliable than the 20amp alternators or is it more of a weight and money thing? Sorry if I derailed the original posters thread. I appreciate any feedback you all might have to offer. Read the notes that go with the Z-figures. The whole purpose of a standby alternator and e-bus is to maximize conservation of energy in the EN ROUTE mode of flight. How may electro-whizzies to you NEED to comfortably achieve the descent/approach waypoint? If you've turned a lot of stuff OFF . . . total loads en route loads below 8A, then you have all the battery's capacity in reserve for approach to landing when you turn everything on that's useful for comfortable termination of the flight. This is what the load analysis sheets are all about on the website. In the RARE instance that you DO need to conserve power, have a check-list driven plan-B to keep it from becoming an emergency. Odds are, you don't need much hardware to get you to the destination airport traffic area. Z-13/8 is probably suited to 99% of all OBAM aircraft flying if the owner/operator takes the time to craft and implement a minimal power en-route mode of energy consumption. The airplanes I've rented didn't have standby alternators or e-busses. Yet, loss of the alternator was not going to have me looking for the asphalt 5 miles away. Here's my "ebus" for TC aircraft. http://tinyurl.com/ok7sjzt I shut the whole electrical system down and leave it off until time to enter the traffic area. An e-bus running 13.5A is not an ENDURANCE BUS. My suggestion to you is assume Z-13/8 and then see if you can get total running loads below 8A . . . actually 10A can probably be supported without seriously discharging the battery.
Bob . . . Quote: |
href="http://www.matronics.com/Navigator?AeroElectric-List" class="">http://www.matronics.com/Navigator?AeroElectric-List
class="">http://forums.matronics.com
class="">http://www.matronics.com/contribution
|
|
[quote][b]
| - The Matronics AeroElectric-List Email Forum - | | Use the List Feature Navigator to browse the many List utilities available such as the Email Subscriptions page, Archive Search & Download, 7-Day Browse, Chat, FAQ, Photoshare, and much more:
http://www.matronics.com/Navigator?AeroElectric-List |
|
|
|
Back to top |
|
 |
Jump4way
Joined: 18 May 2015 Posts: 14
|
Posted: Thu Aug 20, 2015 12:48 pm Post subject: Re: electrical system planning |
|
|
Thanks for the replies. I'll get to work seeing if there is a way to reduce the EBUS load to something more manageable. Like original poster, If I reduce down to only the items essential to keep the engine running, I'll be at 10amps so that alone says that the SD8 alternator is not my best option. I also need to get a handle on the total load required for each of the busses. If I can keep that under the 20-30 amps that the backup alternators can provide then the decisions seem more simplified.
[/quote]I once offered a Z-13/20 utilizing the
SD-20 . . . kinda messy and I pulled it.
I might do some asphalt-cogitation on another
pass at it.[/quote]
I would certainly be interested to see a Z-13/20 if you get the time to put it together.
I like the idea of being able to load shed items by simply closing off the master switch. It seems what I'm learning from reading these forums and Bob's book that I could put items essential for flght (EFII primary coil, ECU 88, and primary fuel pump) on the battery bus. The decisions come on what additional items to put on the EBUS. I think the EBUS could be used as a place to power the additional items that help assure a safe outcome of the flight such as GPS for nagivation, One Comm, autopilot servos and EFIS. All of the other items could be on the main buss such as Flaps, landing and nav lights, trim motors, transponder, 12V outlet, USB charging, Cabin lights, and secondary EFII Coil pump and ECU). This plan would allow quickly load shedding everything on the main buss in the event of a dual alternator failure. I think Z12 will allow this. Does this plan sound reasonable or am I approaching this from the wrong angle?
| - The Matronics AeroElectric-List Email Forum - | | Use the List Feature Navigator to browse the many List utilities available such as the Email Subscriptions page, Archive Search & Download, 7-Day Browse, Chat, FAQ, Photoshare, and much more:
http://www.matronics.com/Navigator?AeroElectric-List |
|
|
|
Back to top |
|
 |
|
|
You cannot post new topics in this forum You cannot reply to topics in this forum You cannot edit your posts in this forum You cannot delete your posts in this forum You cannot vote in polls in this forum You cannot attach files in this forum You can download files in this forum
|
Powered by phpBB © 2001, 2005 phpBB Group
|