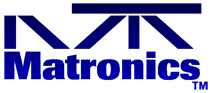 |
Matronics Email Lists Web Forum Interface to the Matronics Email Lists
|
View previous topic :: View next topic |
Author |
Message |
Bob Marshall
Joined: 23 Dec 2010 Posts: 3
|
Posted: Wed Feb 02, 2011 6:58 am Post subject: wire squash connections |
|
|
I plan to use p-mags and the installation instructions show the connections made to the controller are simply striped wire leads placed under screws. Since this is under the cowl, I was hoping that there was a better way. Is there a crimped terminal that could be used along with some heat shrink tubing?
My first post here though I have been reading for a while. Thanks,
Bob
I would post a photo but I cannot figure how to do it.
| - The Matronics AeroElectric-List Email Forum - | | Use the List Feature Navigator to browse the many List utilities available such as the Email Subscriptions page, Archive Search & Download, 7-Day Browse, Chat, FAQ, Photoshare, and much more:
http://www.matronics.com/Navigator?AeroElectric-List |
|
_________________ RV-6A construction resumed. Planning electrical and building wing. |
|
Back to top |
|
 |
rlborger(at)mac.com Guest
|
Posted: Wed Feb 02, 2011 7:42 am Post subject: wire squash connections |
|
|
Bob,
Interesting. I plan to put a pair of P-Mags on the Lycoming for my Toot.
Rather than bare wires under a screw, I'd think about crimping a suitably sized ring terminal onto the wire with proper shrink tube and placing the ring under the screw along with a lock washer.
Others, please chime in if there's an error in my thinking as it's info I'll eventually need.
Thanks,
Bob Borger
Europa Kit #A221 N914XL, XS Tri-Gear, Intercooled 914, Airmaster C/S Prop
http://www.europaowners.org/forums/gallery2.php?g2_itemId=60232
http://www.biplaneforumgallery.com/index.php?cat=10046
Europa Flying!
3705 Lynchburg Dr.
Corinth, TX 76208
Home: 940-497-2123
Cel: 817-992-1117
On Feb 2, 2011, at 8:58, Bob Marshall wrote:
Quote: |
I plan to use p-mags and the installation instructions show the connections made to the controller are simply striped wire leads placed under screws. Since this is under the cowl, I was hoping that there was a better way. Is there a crimped terminal that could be used along with some heat shrink tubing?
My first post here though I have been reading for a while. Thanks,
Bob
I would post a photo but I cannot figure how to do it.
--------
RV-6A construction resumed. Planning electrical and building wing.
Read this topic online here:
http://forums.matronics.com/viewtopic.php?p=329292#329292
|
| - The Matronics AeroElectric-List Email Forum - | | Use the List Feature Navigator to browse the many List utilities available such as the Email Subscriptions page, Archive Search & Download, 7-Day Browse, Chat, FAQ, Photoshare, and much more:
http://www.matronics.com/Navigator?AeroElectric-List |
|
|
|
Back to top |
|
 |
nuckolls.bob(at)aeroelect Guest
|
Posted: Wed Feb 02, 2011 2:26 pm Post subject: wire squash connections |
|
|
At 09:58 AM 2/2/2011, you wrote:
Quote: |
<marshall6916(at)sbcglobal.net>
I plan to use p-mags and the installation instructions show the
connections made to the controller are simply striped wire leads
placed under screws. Since this is under the cowl, I was hoping
that there was a better way. Is there a crimped terminal that could
be used along with some heat shrink tubing?
|
Yeah, my biggest disappointment with that product.
Their service experience with that configuration must
be okay . . . that's what they've used since day one.
Crimping the appendage of some sort of terminal in
those connections might be a bit better than just
crimping the wire . . . but not much.
My best suggestion is to strip leads (20AWG)
to proper length and then 'comb' them such
that they all lay parallel to each other. Then
connect with as much torque on the screws as
you dare.
Try to support the bundles within a few inches
of where they connect with the ignition modules.
Bob . . .
| - The Matronics AeroElectric-List Email Forum - | | Use the List Feature Navigator to browse the many List utilities available such as the Email Subscriptions page, Archive Search & Download, 7-Day Browse, Chat, FAQ, Photoshare, and much more:
http://www.matronics.com/Navigator?AeroElectric-List |
|
|
|
Back to top |
|
 |
raymondj(at)frontiernet.n Guest
|
Posted: Wed Feb 02, 2011 3:37 pm Post subject: wire squash connections |
|
|
do not archive
General question on wires under screws. Is there any benefit in using
an antioxidant similar to what is used on Al wire in electrical panels.
Perhaps not best but better than without?
Raymond Julian
Kettle River, MN
On 02/02/2011 03:22 PM, Robert L. Nuckolls, III wrote:
Quote: |
<nuckolls.bob(at)aeroelectric.com>
At 09:58 AM 2/2/2011, you wrote:
>
> <marshall6916(at)sbcglobal.net>
>
> I plan to use p-mags and the installation instructions show the
> connections made to the controller are simply striped wire leads
> placed under screws. Since this is under the cowl, I was hoping that
> there was a better way. Is there a crimped terminal that could be used
> along with some heat shrink tubing?
Yeah, my biggest disappointment with that product.
Their service experience with that configuration must
be okay . . . that's what they've used since day one.
Crimping the appendage of some sort of terminal in
those connections might be a bit better than just
crimping the wire . . . but not much.
My best suggestion is to strip leads (20AWG)
to proper length and then 'comb' them such
that they all lay parallel to each other. Then
connect with as much torque on the screws as
you dare.
Try to support the bundles within a few inches
of where they connect with the ignition modules.
Bob . . .
|
| - The Matronics AeroElectric-List Email Forum - | | Use the List Feature Navigator to browse the many List utilities available such as the Email Subscriptions page, Archive Search & Download, 7-Day Browse, Chat, FAQ, Photoshare, and much more:
http://www.matronics.com/Navigator?AeroElectric-List |
|
|
|
Back to top |
|
 |
nuckolls.bob(at)aeroelect Guest
|
Posted: Wed Feb 02, 2011 5:12 pm Post subject: wire squash connections |
|
|
At 10:26 AM 2/2/2011, you wrote:
Quote: | --> AeroElectric-List message posted by: Robert Borger <rlborger(at)mac.com>
Bob,
Interesting. I plan to put a pair of P-Mags on the Lycoming for my Toot.
Rather than bare wires under a screw, I'd think about crimping a suitably sized ring terminal onto the wire with proper shrink tube and placing the ring under the screw along with a lock washer.
Others, please chime in if there's an error in my thinking as it's info I'll eventually need. |
Just so we're all on the same page . . .
The twist-n-squash terminal strips featured in this
thread are probably the best there is for taking
wires to etched circuit boards with convenience,
minimum cost and reliability . . . UNDER CERTAIN
CONDITIONS. Here's one example of the technology:
[img]cid:.0[/img]
Here's one of my favorite $100 data acquisition modules that
uses the same terminal strip.
[img]cid:.1[/img]
Note that the bared end of a wire is NOT captured by
a head of the mash-screw . . .
[img]cid:.2[/img]
But by the END of the mash-screw. Further, there is a buffer
strip between the wire strands and the end of the screw. If one
REALLY needs to use a twist-n-squash technology, this is one of
the best.
Legacy design goals for aviation (and other disciplines)
have adopted processes that offer gas-tightness in the
metallic joints of the current carrying pathway along
with wire support immediately adjacent to the gas-tight
joint that prevents failure of the wire under vibration.
Without getting in too much of a dither about new design
goals, I think the best application of this process calls
for parallel strands of wire pressed into the lower
concave surface of the cavity with force from above
offered by the screw. Then supply bundle support within
a couple inches of the squash-joints.
Note that is NOT what I did on this particular example . . .
but then this DAM isn't expected to be in place and
functioning after what we hope is decades of otherwise
unattended service.
Bob . . .
| - The Matronics AeroElectric-List Email Forum - | | Use the List Feature Navigator to browse the many List utilities available such as the Email Subscriptions page, Archive Search & Download, 7-Day Browse, Chat, FAQ, Photoshare, and much more:
http://www.matronics.com/Navigator?AeroElectric-List |
|
Description: |
|
Filesize: |
174.27 KB |
Viewed: |
15710 Time(s) |
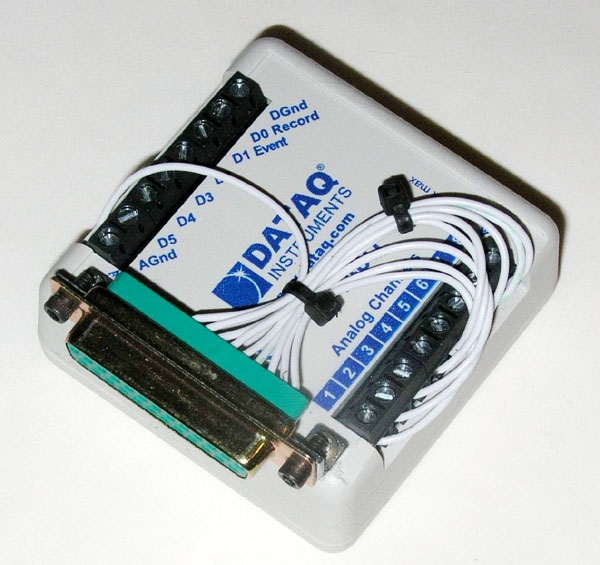
|
Description: |
|
Filesize: |
90.36 KB |
Viewed: |
15710 Time(s) |
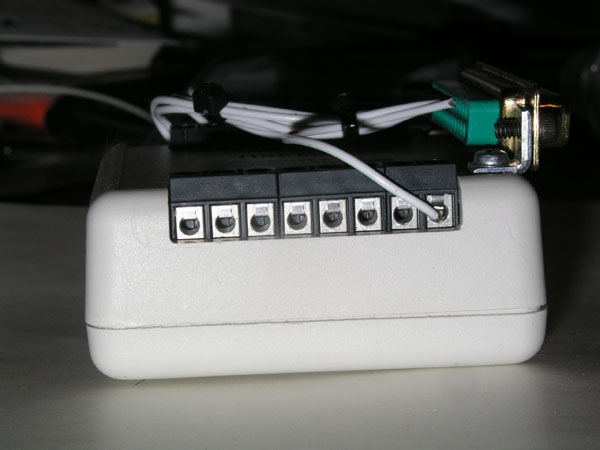
|
Description: |
|
Filesize: |
153.42 KB |
Viewed: |
15710 Time(s) |
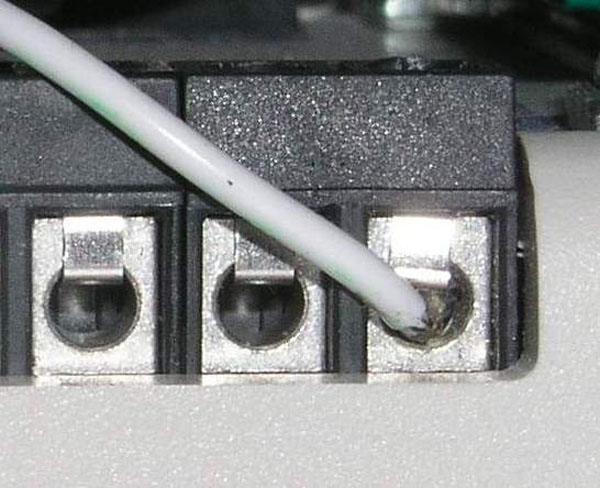
|
|
|
Back to top |
|
 |
rlborger(at)mac.com Guest
|
Posted: Wed Feb 02, 2011 5:44 pm Post subject: wire squash connections |
|
|
Bob,
Oh, OK. Now I see (literally) what was being talked about.
Not the "wrap the wire around the screw and tighten" kind of under screw.
Would crimping a D-Sub female connector pin onto the end of the wire and adding a couple layers of shrink tube over the junction for some stress relief provide a better item to be pressed under the screw? Again assuming you would provide some wire support close to the box.
Thanks,
Bob
On Feb 2, 2011, at 17:25, Robert L. Nuckolls, III wrote:
Quote: | At 10:26 AM 2/2/2011, you wrote:
Quote: | --> AeroElectric-List message posted by: Robert Borger <rlborger(at)mac.com (rlborger(at)mac.com)>
Bob,
Interesting. I plan to put a pair of P-Mags on the Lycoming for my Toot.
Rather than bare wires under a screw, I'd think about crimping a suitably sized ring terminal onto the wire with proper shrink tube and placing the ring under the screw along with a lock washer.
Others, please chime in if there's an error in my thinking as it's info I'll eventually need. |
Just so we're all on the same page . . .
The twist-n-squash terminal strips featured in this
thread are probably the best there is for taking
wires to etched circuit boards with convenience,
minimum cost and reliability . . . UNDER CERTAIN
CONDITIONS. Here's one example of the technology:
<1e81a25b.jpg>
Here's one of my favorite $100 data acquisition modules that
uses the same terminal strip.
<1e81a2d8.jpg>
Note that the bared end of a wire is NOT captured by
a head of the mash-screw . . .
<1e81a345.jpg>
But by the END of the mash-screw. Further, there is a buffer
strip between the wire strands and the end of the screw. If one
REALLY needs to use a twist-n-squash technology, this is one of
the best.
Legacy design goals for aviation (and other disciplines)
have adopted processes that offer gas-tightness in the
metallic joints of the current carrying pathway along
with wire support immediately adjacent to the gas-tight
joint that prevents failure of the wire under vibration.
Without getting in too much of a dither about new design
goals, I think the best application of this process calls
for parallel strands of wire pressed into the lower
concave surface of the cavity with force from above
offered by the screw. Then supply bundle support within
a couple inches of the squash-joints.
Note that is NOT what I did on this particular example . . .
but then this DAM isn't expected to be in place and
functioning after what we hope is decades of otherwise
unattended service.
Bob . . .
|
| - The Matronics AeroElectric-List Email Forum - | | Use the List Feature Navigator to browse the many List utilities available such as the Email Subscriptions page, Archive Search & Download, 7-Day Browse, Chat, FAQ, Photoshare, and much more:
http://www.matronics.com/Navigator?AeroElectric-List |
|
|
|
Back to top |
|
 |
nuckolls.bob(at)aeroelect Guest
|
Posted: Wed Feb 02, 2011 6:24 pm Post subject: wire squash connections |
|
|
Quote: |
Would crimping a D-Sub female connector pin onto the end of the wire
and adding a couple layers of shrink tube over the junction for some
stress relief provide a better item to be pressed under the
screw? Again assuming you would provide some wire support close to the box.
|
That might 'protect' the wire but now you
have a single, solid, small diameter being
captured between two surfaces having a larger
radius. I.e., potentially less contact surface
area than one could get with a compressed
stack of wire strands (19 of them when it
comes to legacy standard wire).
The guys who designed this terminal strip
were no dummies. It's really a pretty well
thought out product. But I'd bet that they
would not recommend that it be used under
the cowl on any vehicle. Not recommending
doesn't make it automatically "bad" . . .
just not the best we know how to do. I
think the risks are low.
One could use PIDG 'pins' . . .
http://search.digikey.com/scripts/DkSearch/dksus.dll?Detail&name=165168-ND
Bob . . .
| - The Matronics AeroElectric-List Email Forum - | | Use the List Feature Navigator to browse the many List utilities available such as the Email Subscriptions page, Archive Search & Download, 7-Day Browse, Chat, FAQ, Photoshare, and much more:
http://www.matronics.com/Navigator?AeroElectric-List |
|
|
|
Back to top |
|
 |
nuckolls.bob(at)aeroelect Guest
|
Posted: Wed Feb 02, 2011 6:27 pm Post subject: wire squash connections |
|
|
At 06:12 PM 2/2/2011, you wrote:
Quote: |
do not archive
General question on wires under screws. Is there any benefit in
using an antioxidant similar to what is used on Al wire in
electrical panels. Perhaps not best but better than without?
|
Probably wouldn't hurt . . . but unless
we're talking about a really bad(at)#$(at)
environment (salt air on sea-going boat?)
I can't imagine that it would help.
Bob . . .
| - The Matronics AeroElectric-List Email Forum - | | Use the List Feature Navigator to browse the many List utilities available such as the Email Subscriptions page, Archive Search & Download, 7-Day Browse, Chat, FAQ, Photoshare, and much more:
http://www.matronics.com/Navigator?AeroElectric-List |
|
|
|
Back to top |
|
 |
dsvs(at)ca.rr.com Guest
|
|
Back to top |
|
 |
dsvs(at)ca.rr.com Guest
|
Posted: Wed Feb 02, 2011 8:09 pm Post subject: wire squash connections |
|
|
You will need to reattach the "els" to the link on the allied web site
--
| - The Matronics AeroElectric-List Email Forum - | | Use the List Feature Navigator to browse the many List utilities available such as the Email Subscriptions page, Archive Search & Download, 7-Day Browse, Chat, FAQ, Photoshare, and much more:
http://www.matronics.com/Navigator?AeroElectric-List |
|
|
|
Back to top |
|
 |
rlborger(at)mac.com Guest
|
Posted: Wed Feb 02, 2011 8:26 pm Post subject: wire squash connections |
|
|
Bob,
Yes, I can see the PIGD pin working.
If contact area is the issue, how about crimp on male spade? Lots of contact area for the screw to mash into. It has a crimp onto the wire and a crimp onto the insulation. Add some heat shrink tubing for strain relief and support the wire.
Bob
On Feb 2, 2011, at 7:20 PM, Robert L. Nuckolls, III wrote:
Quote: |
>
> Would crimping a D-Sub female connector pin onto the end of the wire and adding a couple layers of shrink tube over the junction for some stress relief provide a better item to be pressed under the screw? Again assuming you would provide some wire support close to the box.
That might 'protect' the wire but now you
have a single, solid, small diameter being
captured between two surfaces having a larger
radius. I.e., potentially less contact surface
area than one could get with a compressed
stack of wire strands (19 of them when it
comes to legacy standard wire).
The guys who designed this terminal strip
were no dummies. It's really a pretty well
thought out product. But I'd bet that they
would not recommend that it be used under
the cowl on any vehicle. Not recommending
doesn't make it automatically "bad" . . .
just not the best we know how to do. I
think the risks are low.
One could use PIDG 'pins' . . .
http://search.digikey.com/scripts/DkSearch/dksus.dll?Detail&name=165168-ND
Bob . . .
|
| - The Matronics AeroElectric-List Email Forum - | | Use the List Feature Navigator to browse the many List utilities available such as the Email Subscriptions page, Archive Search & Download, 7-Day Browse, Chat, FAQ, Photoshare, and much more:
http://www.matronics.com/Navigator?AeroElectric-List |
|
|
|
Back to top |
|
 |
nuckolls.bob(at)aeroelect Guest
|
Posted: Wed Feb 02, 2011 9:27 pm Post subject: wire squash connections |
|
|
At 11:22 PM 2/2/2011, you wrote:
Quote: |
Bob,
Yes, I can see the PIGD pin working.
If contact area is the issue, how about crimp on male spade? Lots
of contact area for the screw to mash into. It has a crimp onto the
wire and a crimp onto the insulation. Add some heat shrink tubing
for strain relief and support the wire.
|
I like the pins better . . . or simply
the combed strands.
Bob . . .
| - The Matronics AeroElectric-List Email Forum - | | Use the List Feature Navigator to browse the many List utilities available such as the Email Subscriptions page, Archive Search & Download, 7-Day Browse, Chat, FAQ, Photoshare, and much more:
http://www.matronics.com/Navigator?AeroElectric-List |
|
|
|
Back to top |
|
 |
Bob Marshall
Joined: 23 Dec 2010 Posts: 3
|
Posted: Wed Feb 02, 2011 9:31 pm Post subject: Re: wire squash connections |
|
|
Great suggestions, thanks everyone!! I think I will order the ferrules from Allied though they come in packs of 100. If I do order, does anyone want a few?
My thinking is that the ferrules will do as advertised and prevent strand breaks and maybe a bit of oxidation, too. Just seems like a better connection.
edit:
I just read that the ferrules take a special crimper. oh well, back to the drawing board.
| - The Matronics AeroElectric-List Email Forum - | | Use the List Feature Navigator to browse the many List utilities available such as the Email Subscriptions page, Archive Search & Download, 7-Day Browse, Chat, FAQ, Photoshare, and much more:
http://www.matronics.com/Navigator?AeroElectric-List |
|
_________________ RV-6A construction resumed. Planning electrical and building wing. |
|
Back to top |
|
 |
mikerv6a(at)ao-cs.com Guest
|
Posted: Wed Feb 02, 2011 9:46 pm Post subject: wire squash connections |
|
|
Wire termination ferrules are designed for use in
connectors of the type used in P-Mags.
See digikey.com, part number 298-10044-ND for an example.
These ferrules are tin-plated copper, and they provide
an insulated segment that keeps the wire bend away from
the stripped part of the wire- this helps to prevent
flexing that can break individual wire strands.
The ferrule crimper (yes, another tool...) leaves
flat sides on the ferrule that align with the
clamp action of the terminal into which the ferrule
is inserted.
Ferrules are sized for various wire gauges, the part
number that I gave above is for #18. Ferrules are
available to receive two conductors, having a double-
width insulation sleeve. Catalogs often contain part
numbers that offer various ferrule tube lengths, but
the small connectors that are used on P-Mags would
probably lead to trimming the longer ferrules to fit,
which is OK.
I think that this approach is more desirable than the
PIDG pins, because the ferrule can be trimmed to length
so that the ferrule fits quite neatly into the receiving
area of the connector body, leaving the ferrule's insulator
supported within the box-shaped entry to the connector.
PIDG pins have enough bulk that, in some of these kinds
of connectors, the pin projects outside the confines of
the connector body: This means that the pin is essentially
a miniature cantilevered beam carrying whatever bending
load that might exist in the wire's installation. In the
long run this might result in flexing and breakage of
the PIDG pin.
Mike Linse
Corvallis, OR
Quote: |
Bob,
Yes, I can see the PIGD pin working.
If contact area is the issue, how about crimp on male spade? Lots of
contact area for the screw to mash into. It has a crimp onto the wire and
a crimp onto the insulation. Add some heat shrink tubing for strain
relief and support the wire.
Bob
On Feb 2, 2011, at 7:20 PM, Robert L. Nuckolls, III wrote:
>
> <nuckolls.bob(at)aeroelectric.com>
>>
>> Would crimping a D-Sub female connector pin onto the end of the wire
>> and adding a couple layers of shrink tube over the junction for some
>> stress relief provide a better item to be pressed under the screw?
>> Again assuming you would provide some wire support close to the box.
>
> That might 'protect' the wire but now you
> have a single, solid, small diameter being
> captured between two surfaces having a larger
> radius. I.e., potentially less contact surface
> area than one could get with a compressed
> stack of wire strands (19 of them when it
> comes to legacy standard wire).
>
> The guys who designed this terminal strip
> were no dummies. It's really a pretty well
> thought out product. But I'd bet that they
> would not recommend that it be used under
> the cowl on any vehicle. Not recommending
> doesn't make it automatically "bad" . . .
> just not the best we know how to do. I
> think the risks are low.
>
> One could use PIDG 'pins' . . .
>
> http://search.digikey.com/scripts/DkSearch/dksus.dll?Detail&name=165168-ND
>
> Bob . . .
|
| - The Matronics AeroElectric-List Email Forum - | | Use the List Feature Navigator to browse the many List utilities available such as the Email Subscriptions page, Archive Search & Download, 7-Day Browse, Chat, FAQ, Photoshare, and much more:
http://www.matronics.com/Navigator?AeroElectric-List |
|
|
|
Back to top |
|
 |
dsvs(at)ca.rr.com Guest
|
Posted: Wed Feb 02, 2011 9:56 pm Post subject: wire squash connections |
|
|
Bob I use them on my P-MAGS. Like Bob N says these will not form gas tight
connections in screw down devices, but they do provide a fairly lagre
contact area and they keep the wire from being stressed. I check mine every
condition inspection. So far I have not needed to replace any wires but it
will be easy when the time comes. I wish that the P_MAGS came with D-SUB
connectors, but I am not holding my breath. Don
--
| - The Matronics AeroElectric-List Email Forum - | | Use the List Feature Navigator to browse the many List utilities available such as the Email Subscriptions page, Archive Search & Download, 7-Day Browse, Chat, FAQ, Photoshare, and much more:
http://www.matronics.com/Navigator?AeroElectric-List |
|
|
|
Back to top |
|
 |
bbradburry(at)bellsouth.n Guest
|
Posted: Thu Feb 03, 2011 3:19 am Post subject: wire squash connections |
|
|
If it is an experimental plane, put some on if you want.
Bill B
--
| - The Matronics AeroElectric-List Email Forum - | | Use the List Feature Navigator to browse the many List utilities available such as the Email Subscriptions page, Archive Search & Download, 7-Day Browse, Chat, FAQ, Photoshare, and much more:
http://www.matronics.com/Navigator?AeroElectric-List |
|
|
|
Back to top |
|
 |
mrspudandcompany(at)veriz Guest
|
Posted: Thu Feb 03, 2011 6:50 am Post subject: wire squash connections |
|
|
Quote: | >If contact area is the issue, how about crimp on male spade? Lots of
>contact area for the screw to mash into. It has a crimp onto the wire and
>a crimp onto the insulation. Add some heat shrink tubing for strain
>relief and support the wire.
I like the pins better . . . or simply
the combed strands.
Bob . . .
|
Where I used to work we used a similar terminal in one of our
devices. We used a crimp on pin on the end of the wires before insertion.
This made for a nice looking finished job, But unless the assembly tech
really torqued the screws down very tight, they would tend to loosen.
Roger
| - The Matronics AeroElectric-List Email Forum - | | Use the List Feature Navigator to browse the many List utilities available such as the Email Subscriptions page, Archive Search & Download, 7-Day Browse, Chat, FAQ, Photoshare, and much more:
http://www.matronics.com/Navigator?AeroElectric-List |
|
|
|
Back to top |
|
 |
ainut(at)knology.net Guest
|
Posted: Thu Feb 03, 2011 8:53 am Post subject: wire squash connections |
|
|
Bob, can you tell if the Labjack U12, www.labjack.com/U12 , is
suitable? I had no idea that termination was such a concern. I've had
the U12 for several years and hope to use it in my Mustang II
(Mustang2.) It was only $100 at the time I bought it as well. If I
need to get the dataq part, so be it, but it doesn't has have as many
capabilities as the Labjack.
Thanks,
David M.
Robert L. Nuckolls, III wrote:
Quote: | At 10:26 AM 2/2/2011, you wrote:
>
>
> Bob,
>
> Interesting. I plan to put a pair of P-Mags on the Lycoming for my
> Toot.
>
> Rather than bare wires under a screw, I'd think about crimping a
> suitably sized ring terminal onto the wire with proper shrink tube
> and placing the ring under the screw along with a lock washer.
>
> Others, please chime in if there's an error in my thinking as it's
> info I'll eventually need.
Just so we're all on the same page . . .
The twist-n-squash terminal strips featured in this
thread are probably the best there is for taking
wires to etched circuit boards with convenience,
minimum cost and reliability . . . UNDER CERTAIN
CONDITIONS. Here's one example of the technology:
Emacs!
Here's one of my favorite $100 data acquisition modules that
uses the same terminal strip.
Emacs!
Note that the bared end of a wire is NOT captured by
a head of the mash-screw . . .
Emacs!
But by the END of the mash-screw. Further, there is a buffer
strip between the wire strands and the end of the screw. If one
REALLY needs to use a twist-n-squash technology, this is one of
the best.
Legacy design goals for aviation (and other disciplines)
have adopted processes that offer gas-tightness in the
metallic joints of the current carrying pathway along
with wire support immediately adjacent to the gas-tight
joint that prevents failure of the wire under vibration.
Without getting in too much of a dither about new design
goals, I think the best application of this process calls
for parallel strands of wire pressed into the lower
concave surface of the cavity with force from above
offered by the screw. Then supply bundle support within
a couple inches of the squash-joints.
Note that is NOT what I did on this particular example . . .
but then this DAM isn't expected to be in place and
functioning after what we hope is decades of otherwise
unattended service.
Bob . . .
|
--
If you're an American, just say NO to the Obamanation, to socialism, and get rid of Soros.
| - The Matronics AeroElectric-List Email Forum - | | Use the List Feature Navigator to browse the many List utilities available such as the Email Subscriptions page, Archive Search & Download, 7-Day Browse, Chat, FAQ, Photoshare, and much more:
http://www.matronics.com/Navigator?AeroElectric-List |
|
|
|
Back to top |
|
 |
nuckolls.bob(at)aeroelect Guest
|
Posted: Thu Feb 03, 2011 1:01 pm Post subject: wire squash connections |
|
|
At 11:45 AM 2/3/2011, you wrote:
Quote: |
Bob, can you tell if the Labjack U12, www.labjack.com/U12 , is
suitable? I had no idea that termination was such a concern. I've
had the U12 for several years and hope to use it in my Mustang II
(Mustang2.) It was only $100 at the time I bought it as well.
|
Suitable for what task? How do you intend to use
the device and what effects might failure of the
device have on the outcome of any given flight.
I believe the U12 is available as a bare-foot board
assembly that has no i/o terminal strip or housing.
You can solder your own i/o termination technology
to the board. But even so, you need to think through
the FMEA for having this board fail to accomplish
any given task.
If I need to get the dataq part, so be it, but it doesn't has have as
many capabilities as the Labjack.
The DataQ device has the SAME terminal strips. The
pictures showed how I reduced the inconvenience of
of those strips with a D-sub connection adaptation . . .
but the strips are still there.
Unless you're using this board to develop feedback
data for an autopilot or fuel injection system,
then I suspect that failure to perform is nothing
worse than a maintenance event. EITHER product will
offer good value.
Bob . . .
| - The Matronics AeroElectric-List Email Forum - | | Use the List Feature Navigator to browse the many List utilities available such as the Email Subscriptions page, Archive Search & Download, 7-Day Browse, Chat, FAQ, Photoshare, and much more:
http://www.matronics.com/Navigator?AeroElectric-List |
|
|
|
Back to top |
|
 |
ainut(at)knology.net Guest
|
Posted: Thu Feb 03, 2011 5:02 pm Post subject: wire squash connections |
|
|
My purposes for this unit are pressures (turbo (3), air(2), water, and
oil), misc switches, and possibly duct placements with the analog outs.
I also intend to use the AMD 494/495 chips with thermocouples for
temps. No system critical functions will be used with this a/d unit.
I intend to use a megasquirt family device for engine controls and rpm
reporting, etc.
Thanks,
David
Robert L. Nuckolls, III wrote:
Quote: |
<nuckolls.bob(at)aeroelectric.com>
At 11:45 AM 2/3/2011, you wrote:
>
>
> Bob, can you tell if the Labjack U12, www.labjack.com/U12 , is
> suitable? I had no idea that termination was such a concern. I've
> had the U12 for several years and hope to use it in my Mustang II
> (Mustang2.) It was only $100 at the time I bought it as well.
Suitable for what task? How do you intend to use
the device and what effects might failure of the
device have on the outcome of any given flight.
I believe the U12 is available as a bare-foot board
assembly that has no i/o terminal strip or housing.
You can solder your own i/o termination technology
to the board. But even so, you need to think through
the FMEA for having this board fail to accomplish
any given task.
If I need to get the dataq part, so be it, but it doesn't has have as
many capabilities as the Labjack.
The DataQ device has the SAME terminal strips. The
pictures showed how I reduced the inconvenience of
of those strips with a D-sub connection adaptation . . .
but the strips are still there.
Unless you're using this board to develop feedback
data for an autopilot or fuel injection system,
then I suspect that failure to perform is nothing
worse than a maintenance event. EITHER product will
offer good value.
Bob . . .
|
--
If you're an American, just say NO to the Obamanation, to socialism, and get rid of Soros.
| - The Matronics AeroElectric-List Email Forum - | | Use the List Feature Navigator to browse the many List utilities available such as the Email Subscriptions page, Archive Search & Download, 7-Day Browse, Chat, FAQ, Photoshare, and much more:
http://www.matronics.com/Navigator?AeroElectric-List |
|
|
|
Back to top |
|
 |
|
|
You cannot post new topics in this forum You cannot reply to topics in this forum You cannot edit your posts in this forum You cannot delete your posts in this forum You cannot vote in polls in this forum You cannot attach files in this forum You can download files in this forum
|
Powered by phpBB © 2001, 2005 phpBB Group
|