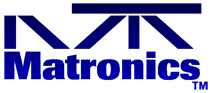 |
Matronics Email Lists Web Forum Interface to the Matronics Email Lists
|
View previous topic :: View next topic |
Author |
Message |
digidocs
Joined: 04 Dec 2013 Posts: 60
|
Posted: Wed Jan 08, 2014 10:19 am Post subject: Thoughts on a few electrical system configurations? |
|
|
I'm nearing the point in my RV-10 build where I need to make some decisions about the electrical system architecture. Also, like any good engineer, I've got a serious case of analysis paralysis going. In an effort to help clear the logjam, would the list share its collective thoughts?
Background
- I fly in IMC fairly regularly.
- The engine doesn't require power to keep running, but the attitude instruments are all electrically powered. Thus keeping at least some power running is important. (i.e.: AI, GPS, COM)
- The planned avionics configuration is such that in a split bus design, one set/bus of units could be depowered without loss of overall functionality. (i.e.: EFIS, GPS1, COM1 on Bus A; AI, GPS2, COM2 on Bus B)
- Any LiFePO4 batteries mounted firewall forward in stainless steel enclosures for fire containment (included in weight estimates).
System objectives
- Provide 4.5A of power for at least 4 hours in the event of any component failure (unless we can point to a *very* established track record of performance for that component)
- Minimize weight
- Minimize complexity and component count
Configuration options and my thoughts:
(weights given are nominal relative to configuration 1)
1. 60A alternator, 27Ah lead acid battery, e-bus. +0 lbs.
Standard configuration on this type of aircraft. According to Bob, complete battery failure is very rare. Even fairly degraded battery has capacity to provide sufficient reserve power. E-bus protects against wiring faults. Simple architecture is a plus. Configuration is (relatively) heavy.
2. 60A alternator, 8A alternator, 17Ah lead acid battery, e-bus. -9 lbs.
Addition of backup alternator allows battery to be reduced in size, saves some weight.
3. 60A alternator, 12Ah LiFePO4 primary battery, 12Ah LiFePO4 backup battery, split bus. -18lbs.
Alternator charges primary battery and, through diode, secondary battery. Split bus design because LiFePO4 batteries have low reliability compared to lead acid. Cost/availability limits backup battery to 12Ah which falls short of endurance requirement, may be possible to reduce power consumption. Relatively simple architecture. Lightest configuration.
4. 60A alternator, 8A alternator, 12Ah LiFePO4 primary battery, 2Ah lead acid secondary battery, split bus. -17lbs.
60A alternator + 12Ah LiFePO4 power Bus A. 8A alternator + 2Ah lead acid power Bus B. Busses are not interconnected. May be safe to mount 2Ah lead acid under panel to reduce firewall penetrations and wiring complexity. Dual alternator, dual battery, split bus provides high availability and unlimited endurance. Medium/high complexity. Relatively light.
5. Same as configuration 4, except with 4Ah LiFePO4 secondary battery. -16lbs.
Presented in case there are issues with using/charging such small lead acid batteries with 8A alternator.
Thanks for your thoughts,
David
| - The Matronics AeroElectric-List Email Forum - | | Use the List Feature Navigator to browse the many List utilities available such as the Email Subscriptions page, Archive Search & Download, 7-Day Browse, Chat, FAQ, Photoshare, and much more:
http://www.matronics.com/Navigator?AeroElectric-List |
|
|
|
Back to top |
|
 |
Mauledriver(at)nc.rr.com Guest
|
Posted: Wed Jan 08, 2014 1:40 pm Post subject: Thoughts on a few electrical system configurations? |
|
|
David, I'm attaching the main power distribution diagram and
Fuse/Breaker diagram for my RV10 (2.3 years and 350+ hours).
It is an Aeroelectric Z-14 design with (2) 17aH Odysseys, 2
alternators, and dual buses. The panel, designed around 2008, includes
3 GRT/HX EFIS with dual AHRS, a G430w, SL30, PM audio panel, and TT AP.
I like the whole setup. I would be glad to answer any questions about it.
Bill "the electrical and avionics design & build was the most fun part
of the project" Watson
On 1/8/2014 1:19 PM, digidocs wrote:
Quote: |
I'm nearing the point in my RV-10 build where I need to make some decisions about the electrical system architecture. Also, like any good engineer, I've got a serious case of analysis paralysis going. In an effort to help clear the logjam, would the list share its collective thoughts?
Background
- I fly in IMC fairly regularly.
- The engine doesn't require power to keep running, but the attitude instruments are all electrically powered. Thus keeping at least some power running is important. (i.e.: AI, GPS, COM)
- The planned avionics configuration is such that in a split bus design, one set/bus of units could be depowered without loss of overall functionality. (i.e.: EFIS, GPS1, COM1 on Bus A; AI, GPS2, COM2 on Bus B)
- Any LiFePO4 batteries mounted firewall forward in stainless steel enclosures for fire containment (included in weight estimates).
System objectives
- Provide 4.5A of power for at least 4 hours in the event of any component failure (unless we can point to a *very* established track record of performance for that component)
- Minimize weight
- Minimize complexity and component count
Configuration options and my thoughts:
(weights given are nominal relative to configuration 1)
1. 60A alternator, 27Ah lead acid battery, e-bus. +0 lbs.
Standard configuration on this type of aircraft. According to Bob, complete battery failure is very rare. Even fairly degraded battery has capacity to provide sufficient reserve power. E-bus protects against wiring faults. Simple architecture is a plus. Configuration is (relatively) heavy.
2. 60A alternator, 8A alternator, 17Ah lead acid battery, e-bus. -9 lbs.
Addition of backup alternator allows battery to be reduced in size, saves some weight.
3. 60A alternator, 12Ah LiFePO4 primary battery, 12Ah LiFePO4 backup battery, split bus. -18lbs.
Alternator charges primary battery and, through diode, secondary battery. Split bus design because LiFePO4 batteries have low reliability compared to lead acid. Cost/availability limits backup battery to 12Ah which falls short of endurance requirement, may be possible to reduce power consumption. Relatively simple architecture. Lightest configuration.
4. 60A alternator, 8A alternator, 12Ah LiFePO4 primary battery, 2Ah lead acid secondary battery, split bus. -17lbs.
60A alternator + 12Ah LiFePO4 power Bus A. 8A alternator + 2Ah lead acid power Bus B. Busses are not interconnected. May be safe to mount 2Ah lead acid under panel to reduce firewall penetrations and wiring complexity. Dual alternator, dual battery, split bus provides high availability and unlimited endurance. Medium/high complexity. Relatively light.
5. Same as configuration 4, except with 4Ah LiFePO4 secondary battery. -16lbs.
Presented in case there are issues with using/charging such small lead acid batteries with 8A alternator.
Thanks for your thoughts,
David
Read this topic online here:
http://forums.matronics.com/viewtopic.php?p=416700#416700
-----
No virus found in this message.
Checked by AVG - www.avg.com
|
| - The Matronics AeroElectric-List Email Forum - | | Use the List Feature Navigator to browse the many List utilities available such as the Email Subscriptions page, Archive Search & Download, 7-Day Browse, Chat, FAQ, Photoshare, and much more:
http://www.matronics.com/Navigator?AeroElectric-List |
|
Description: |
|
 Download |
Filename: |
Tigressa_Wire_Book_and_Load_Analysis_GRT_-_fuse-centric_V4.1_7-27-13.pdf |
Filesize: |
9.9 KB |
Downloaded: |
317 Time(s) |
Description: |
|
 Download |
Filename: |
Main_Power_Distribution_5.10_10-31-13.pdf |
Filesize: |
35.06 KB |
Downloaded: |
297 Time(s) |
|
|
Back to top |
|
 |
Jim Berry
Joined: 10 Jan 2006 Posts: 237 Location: Denver
|
Posted: Wed Jan 08, 2014 2:37 pm Post subject: Re: Thoughts on a few electrical system configurations? |
|
|
David,
Suggest you also consider 60A primary alt. and 20A secondary alt. Set the regulator on the secondary 0.5V lower than primary regulator. I have this in my all glass RV10. After 3 years, I had a primary alt. failure due to spun bearing shorting out the winding. Bus voltage dropped 0.5V as expected; the secondary alt. picked up the slack and we completed our flight at our leisure. With 20A I can keep everything lit up indefinitely except my heated pitot and landing lights. No bus switching or load shedding necessary.
Jim Berry
RV-10
| - The Matronics AeroElectric-List Email Forum - | | Use the List Feature Navigator to browse the many List utilities available such as the Email Subscriptions page, Archive Search & Download, 7-Day Browse, Chat, FAQ, Photoshare, and much more:
http://www.matronics.com/Navigator?AeroElectric-List |
|
|
|
Back to top |
|
 |
|
|
You cannot post new topics in this forum You cannot reply to topics in this forum You cannot edit your posts in this forum You cannot delete your posts in this forum You cannot vote in polls in this forum You cannot attach files in this forum You can download files in this forum
|
Powered by phpBB © 2001, 2005 phpBB Group
|