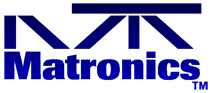 |
Matronics Email Lists Web Forum Interface to the Matronics Email Lists
|
View previous topic :: View next topic |
Author |
Message |
user9253
Joined: 28 Mar 2008 Posts: 1938 Location: Riley TWP Michigan
|
Posted: Mon Jan 12, 2015 8:07 pm Post subject: UN-FUSED MAIN BUS FEEDER |
|
|
It is common practice not to fuse the main bus feeder between the battery and the main power bus. But what about aircraft with small electrical loads and small feeders? For example, the RV-12 typically uses 10 to 15 amps total. The main feeder is 12 awg per the factory plans. This thread, http://www.vansairforce.com/community/showthread.php?t=120999
is about a fire (while on the ground) that was caused by the main feeder shorting out to the choke cable. Do we need to rethink the practice of not fusing the main power feeder? Or are good wiring practices safe enough?
Joe
| - The Matronics AeroElectric-List Email Forum - | | Use the List Feature Navigator to browse the many List utilities available such as the Email Subscriptions page, Archive Search & Download, 7-Day Browse, Chat, FAQ, Photoshare, and much more:
http://www.matronics.com/Navigator?AeroElectric-List |
|
_________________ Joe Gores |
|
Back to top |
|
 |
nuckolls.bob(at)aeroelect Guest
|
Posted: Mon Jan 12, 2015 9:30 pm Post subject: UN-FUSED MAIN BUS FEEDER |
|
|
At 22:07 2015-01-12, you wrote:
Quote: |
It is common practice not to fuse the main bus feeder between the
battery and the main power bus. But what about aircraft with small
electrical loads and small feeders? For example, the RV-12
typically uses 10 to 15 amps total. The main feeder is 12 awg per
the factory plans. This thread,
http://www.vansairforce.com/community/showthread.php?t=120999
is about a fire (while on the ground) that was caused by the main
feeder shorting out to the choke cable. Do we need to rethink the
practice of not fusing the main power feeder? Or are good wiring
practices safe enough?
Joe
|
The FARS speak to the risks for ENGINE CRANKING
feeders where bus feeders are on the same order
of risk as the cranking circuits.
Airplanes that are powered with 'tiny' alternators
tend to have bus feeders to match and are
at greater risk from battery-fed faults. The
thread is extensive and riddled with unclear
and/or erroneous words. I'll need to digest
it a bit . . .
The short answer is that some form of transient
tolerant fault protection wouldn't hurt but better
installation of the potentially vulnerable wire
would be better. So yes, good wiring practices
are the first line of defense against such events.
The fact that this wire became mechanically
compromised speaks to questionable shop practice.
I'll sift through the narrative and report back.
Watch this space.
Bob . . .
| - The Matronics AeroElectric-List Email Forum - | | Use the List Feature Navigator to browse the many List utilities available such as the Email Subscriptions page, Archive Search & Download, 7-Day Browse, Chat, FAQ, Photoshare, and much more:
http://www.matronics.com/Navigator?AeroElectric-List |
|
|
|
Back to top |
|
 |
jluckey(at)pacbell.net Guest
|
Posted: Mon Jan 12, 2015 9:46 pm Post subject: UN-FUSED MAIN BUS FEEDER |
|
|
Joe,
Thanks for bringing this to our attention. Very scary and very interesting. A poster on the VansAirforce forum states that the RV-12 is "certified" under an ASTM standard.
I found this:
ASTM F2245 - 14. Standard Specification for Design and Performance of a Light Sport Airplane. http://www.astm.org/Standards/F2245.htm
The abstract for that document suggests that it discusses electrical systems. I would like to get a look at that document but I'm hesitant to spend $60 just for a look-see.
Does anyone have a copy of that document that I could look at? Has anyone on this forum seen/read that document and would care to comment on it.
Back to the VansAirforce post - The original poster did not post any pictures of the before & after. That's a shame because it might be very instructive if we could see how that feeder was routed.
-Jeff
PS - As long-time members of this forum may recall, I have been a proponent of protecting all feeders and my designs incorporate such protection. This current (no pun intended) issue is a good example of why. If this fire had occurred while airborne the results could have been catastrophic.
On Monday, January 12, 2015 8:24 PM, user9253 <fransew(at)gmail.com> wrote:
--> AeroElectric-List message posted by: "user9253" <fransew(at)gmail.com (fransew(at)gmail.com)>It is common practice not to fuse the main bus feeder between the battery and the main power bus. But what about aircraft with small electrical loads and small feeders? For example, the RV-12 typically uses 10 to 15 amps total. The main feeder is 12 awg per the factory plans. This thread, http://www.vansairforce.com/community/showthread.php?t=120999is about a fire (while on the ground) that was caused by the main feeder shorting out to the choke cable. Do we need to rethink the practice of not fusing the main power feeder? Or are good wiring practices safe enough?Joe--------Joe GoresRead this topic online here:http://forums.matronics.com/viewtopic.php?p=436938#436938
[quote][b]
| - The Matronics AeroElectric-List Email Forum - | | Use the List Feature Navigator to browse the many List utilities available such as the Email Subscriptions page, Archive Search & Download, 7-Day Browse, Chat, FAQ, Photoshare, and much more:
http://www.matronics.com/Navigator?AeroElectric-List |
|
|
|
Back to top |
|
 |
nuckolls.bob(at)aeroelect Guest
|
Posted: Tue Jan 13, 2015 4:09 am Post subject: UN-FUSED MAIN BUS FEEDER |
|
|
At 23:45 2015-01-12, you wrote:
Quote: | Joe,
Thanks for bringing this to our attention. Very scary and very interesting. A poster on the VansAirforce forum states that the RV-12 is "certified" under an ASTM standard.
I found this:
ASTM F2245 - 14. Standard Specification for Design and Performance of a Light Sport Airplane. http://www.astm.org/Standards/F2245.htm
The abstract for that document suggests that it discusses electrical systems. I would like to get a look at that document but I'm hesitant to spend $60 just for a look-see.
Does anyone have a copy of that document that I could look at? Has anyone on this forum seen/read that document and would care to comment on it.
Back to the VansAirforce post - The original poster did not post any pictures of the before & after. That's a shame because it might be very instructive if we could see how that feeder was routed.
-Jeff
PS - As long-time members of this forum may recall, I have been a proponent of protecting all feeders and my designs incorporate such protection. This current (no pun intended) issue is a good example of why. If this fire had occurred while airborne the results could have been catastrophic. |
Yes, there are a constellation of risks associated
with materials and processes for assembling
airplanes. I recall a couple of instances
of fuel fed fires on Glasairs waaayyy back when
with root cause traced to poorly installed
fire wall fittings on fuel lines. An RV8
went down in flames with the pilot electing
to do a no-parachute egress from the aircraft.
Root cause for this unhappy event will never be
known . . . but a whole lot of history and FMEA
practices can give us some good ideas . . . and
I'll bet none of them are mitigated by ADDING
another feature to a proven system. It's more
likely that some simple failure to observe
good practice is the root cause. Missing safety
wire, o-ring pinched, cracked line, etc. etc.
Hard Reality of Life: No amount of ISO9000
documentation and holy-watered work instructions
will guarantee that one of life's little
"Aw S(at)#$s" won't jump up an bite you.
Are you working under the assumption that the
triggering event was a hard faulted 12AWG bus
feeder?
In your hypothesis, how does a relatively young,
robust wire get compromised severely over
a short period of time to produce such
a high energy event?
I'm going to sift through the narrative but
there was one poster to the thread that wondered
about engine grounding. Those control cables
(wound jacket Bowden controls?) are steel and
relatively poor conductors. If the airplane's
engine were not properly bonded to a high integrity
ground system, then the current demands of an engine
start circulating in the control cables offers
a plausible explanation for the energy flows
that triggered the event.
Before we chase the rabbit down the bus-feeder-
protection hole, let's assure ourselves that
it was a hard-faulted WIRE that started the unhappy
event and not a couple of heater-coil control
cables being tasked to do things never intended
by the designers. I am skeptical that a burning
12AWG wire bundled with steel engine controls would
do much damage to them. On the other hand, engine
controls masquerading as crankcase grounds would
not only exhibit severe heat stress, they would
compromise the insulation on wires bundled together
the controls.
I looked at the link for the ATSM document . . .
33 pages for $60 ???? I'm pretty sure Textron
has a subscription to such documents, I'll see
if I can put my hands on one. But at best, it's
an index to a bunch of other documents or at
worst, a gathering of lofty words speaking
to design goals dreamed up by individuals with
little or no experience at the craft.
If you look through the z-figures, you'll see
fusible links at the source end of bus feeders
on 'tiny alternator' airplanes. Airplanes with
big alternators are assumed to carry the same
gage wire throughout the cranking circuit and
bus feeders . . . 4AWG or larger. Probability
of hard faulting a fat wire in a manner that
puts the wire at risk is exceedingly low as
demonstrated in hundreds of thousands of examples
over the last century of aviation history.
The fact that the 12AWG wire in question burned
only ahead of the fire wall suggests that it
came to ground at the fire wall penetration
site. How would/did this happen? Just
for grins . . . connect a 12AWG wire to a
battery grounded to a 'fire wall', run the
wire through a hole in that piece of metal
then work the wire against the edge of the hole
until you produce a fault sufficient to
burn the wire. How much time? How much force?
What kind of motion? What was going on from
the time sparks first started to fly (soft
fault) until connection could be made to
cook the wire? Now, how did this happen in
the event airplane?
The discussion I downloaded last night is
long on supposition and conjecture . . . short
on failure analysis. It seems more likely that the
controls got hot first and compromised the
insulation which triggered an electrical
compromise of the wire but without sifting
the aftermath in a logical and ordered manner,
the facts are elusive.
We need to be sure of the simple-ideas in
physics and proven practices before painting
this event as a justification for pasting
a band-aid on a system that was bleeding
profusely somewhere else.
Bob . . . [quote][b]
| - The Matronics AeroElectric-List Email Forum - | | Use the List Feature Navigator to browse the many List utilities available such as the Email Subscriptions page, Archive Search & Download, 7-Day Browse, Chat, FAQ, Photoshare, and much more:
http://www.matronics.com/Navigator?AeroElectric-List |
|
|
|
Back to top |
|
 |
user9253
Joined: 28 Mar 2008 Posts: 1938 Location: Riley TWP Michigan
|
Posted: Tue Jan 13, 2015 4:05 pm Post subject: Re: UN-FUSED MAIN BUS FEEDER |
|
|
Quote: | Are you working under the assumption that the
triggering event was a hard faulted 12AWG bus
feeder? |
Yes, that is what happened, in my opinion, after reading the builder's description in this post: http://www.vansairforce.com/community/showpost.php?p=945235&postcount=17
Posts by others in that thread are only speculation.
Quote: | In your hypothesis, how does a relatively young,
robust wire get compromised severely over
a short period of time to produce such
a high energy event? |
The #12 awg wire that burned is the main feeder between the contactor and the instrument panel. The wire does NOT run parallel to or with choke or throttle cables through the firewall. Wires in the RV-12 pass through a separate hole in the firewall. The #12 wire runs perpendicular to and under the throttle cables. In my RV-12, there is a half inch space between the #12 wire and throttle cables and both are held apart by cushion clamps. In the accident RV-12, the #12 wire must have been in contact with the underside of a throttle cable. I suspect that the insulation on the wire was abraded by a vibrating throttle cable. The copper wire then welded itself to the steel cable. The builder is adamant that his engine is well grounded and thus had nothing to do with the incident. The Rotax engine starts so quickly, within 1 or 2 seconds, that it seems unlikely that throttle and choke cables would have time to heat up over their entire length to a temperature high enough to melt wire insulation. The Rotax dynamo does not use engine ground for conducting current as would a conventional alternator. The single phase AC output of the dynamo is conducted through two wires to the rectifier/regulator which is mounted on the firewall. After engine start, only engine-instrument-sensor current is dependent on the engine ground. Without having the fire damage to examine, all we have to go by is the post by the pilot-builder. Below is a link to a picture of the wire in question in my airplane, not the accident aircraft. http://tinyurl.com/RV-12-wires
Joe
| - The Matronics AeroElectric-List Email Forum - | | Use the List Feature Navigator to browse the many List utilities available such as the Email Subscriptions page, Archive Search & Download, 7-Day Browse, Chat, FAQ, Photoshare, and much more:
http://www.matronics.com/Navigator?AeroElectric-List |
|
_________________ Joe Gores |
|
Back to top |
|
 |
nuckolls.bob(at)aeroelect Guest
|
Posted: Tue Jan 13, 2015 6:12 pm Post subject: UN-FUSED MAIN BUS FEEDER |
|
|
The #12 awg wire that burned is the main feeder between the contactor and the instrument panel. The wire does NOT run parallel to or with choke or throttle cables through the firewall. Wires in the RV-12 pass through a separate hole in the firewall. The #12 wire runs perpendicular to and under the throttle cables. In my RV-12, there is a half inch space between the #12 wire and throttle cables and both are held apart by cushion clamps. In the accident RV-12, the #12 wire must have been in contact with the underside of a throttle cable. I suspect that the insulation on the wire was abraded by a vibrating throttle cable. The copper wire then welded itself to the steel cable. The builder is adamant that his engine is well grounded and thus had nothing to do with the incident. The Rotax engine starts so quickly, within 1 or 2 seconds, that it seems unlikely that throttle and choke cables would have time to heat up over their entire length to a temperature high enough to melt wire insulation. The Rotax dynamo does not use engine ground for conducting current as would a conventional alternator. The single phase AC output of the dynamo is conducted through two wires to the rectifier/regulator which is mounted on the firewall. After engine start, only engine-instrument-sensor current is dependent on the engine ground. Without having the fire damage to examine, all we have to go by is the post by the pilot-builder. Below is a link to a picture of the wire in question in my airplane, not the accident aircraft. http://tinyurl.com/RV-12-wires
Joe
Aha! Good data points. Just got a task mailed off to a customer and had time to read the thread downloaded last night.
It seems clear that the wire insulation was compromised against the control cables . . . failure to observe common practice for the maintenance of spacing.
Picked this out of the downloaded thread . . .
On the issue of a fusible link, it is not true that it would create a weak spot electrically. A fusible link will not fail in the event of a spurious spike in current; only in the event of a major, uncontrolled power draw....a short circuit. It is true that it is 4 wire sizes smaller ( or 4 numbers larger); 16 awg in the case of the RV-12 battery power wire. Regarding the philosophy of aircraft design, to wit; the issue of a system failure versus a fire aloft is hardly worth discussion. Seriously? In a VFR, daytime-only RV-12, we'd consider a fire aloft a better deal than a display failure?! I appreciate all the redundant advice to carefully route & shield the battery power wire. Great advice. Took care of it. But that is a separate issue of the wire becoming shorted for whatever unforeseen reason. And there seems to be much naive comment on this blog that if there's a problem, a fuse would blow. It needs to be clearly understood here that if a power wire shorts out in the RV-12, a fantastically dangerous hot spot will result; in essence, an arc welder. That's what I had, and the damage was devastating. Additionally, it needs to be understood that proper engine-to-fuselage grounding will not protect against such a short circuit. My engine is properly grounded, In fact, I long ago took the precaution of an additional ( and very substantial) electrical ground wire. Unprotected +12v current will find ANY path when it "shorts" out. In my case, it virtually welded right through both the throttle & choke cables, as well as destroying the #22 (black) ground wire in the GPS antenna/receiver cable all the way to the connector on the Vans AV-5000A control module in the avionics bay (a $600 piece)
As I mentioned last night, as wire sizes drop out
of the relatively invincible 'fat wire' category,
they do become vulnerable a hard-fault burn. The
fusible link is one way to go. It's compact, inexpensive
and effective. Cars have used them for years but
to my knowledge, the TC aircraft industry has never
embraced them. There's a class of circuit protector
with LONG fusing constants commonly referred to as
a current limiter. The ANL series devices . . .
http://tinyurl.com/k9tmfmh
. . . have been a common ingredient in time-delay,
hard-fault protection for over 70 years. The
automotive industry has used a variety of
heavy-fuses as well. An interesting line
that popped up 30 or so years ago was the
miniature current limiters or MANL series
devices. They're popular with installers
of kilowatt boom boxes in automobiles. They're
readily available from hundreds of sources.
http://tinyurl.com/pcuscp2
I've not seen a MANL holder from the automotive
world that instilled much confidence. Not sure
about the base materials but they're probably
okay. If it were my installation, I'd make base
our of a piece of phenolic or Delrin . . .but
the current limiters are just fine,
Fusible link wire is available in bulk from
a host of automotive supply houses. Here's
one such product
http://tinyurl.com/p3hrq22
The fusible link is mechanically attractive.
Installs with splices, ties right into a wire
bundle with the rest of the wires. If it's in
a bundle, it would e a good thing to add a layer
of silicon impregnated fiberglas sleeving like
that described in my articles and offered in
B&C's fusible link kit.
In any case, protecting light feeders
directly attached to a battery is a good idea.
Bob . . . [quote][b]
| - The Matronics AeroElectric-List Email Forum - | | Use the List Feature Navigator to browse the many List utilities available such as the Email Subscriptions page, Archive Search & Download, 7-Day Browse, Chat, FAQ, Photoshare, and much more:
http://www.matronics.com/Navigator?AeroElectric-List |
|
|
|
Back to top |
|
 |
user9253
Joined: 28 Mar 2008 Posts: 1938 Location: Riley TWP Michigan
|
Posted: Tue Jan 13, 2015 7:12 pm Post subject: Re: UN-FUSED MAIN BUS FEEDER |
|
|
Thanks for your insight, Bob.
Joe
| - The Matronics AeroElectric-List Email Forum - | | Use the List Feature Navigator to browse the many List utilities available such as the Email Subscriptions page, Archive Search & Download, 7-Day Browse, Chat, FAQ, Photoshare, and much more:
http://www.matronics.com/Navigator?AeroElectric-List |
|
_________________ Joe Gores |
|
Back to top |
|
 |
nuckolls.bob(at)aeroelect Guest
|
Posted: Wed Jan 14, 2015 8:21 am Post subject: UN-FUSED MAIN BUS FEEDER |
|
|
Quote: |
In any case, protecting light feeders
directly attached to a battery is a good idea. |
P.S. Keep in mind that there are numerous ways
a failure can take down the main bus. Battery
contactor failure. Failure in controls for
battery contactor . . . as well as any fault
that compromises the main bus feeder.
This is one reason why the e-bus evolved to
the present day. It's a two-feed bus
that not only offers easily accessed, planed
reduction in load. It also offers redundancy
in source paths that negates risks for loss
of main bus.
Bob . . . [quote][b]
| - The Matronics AeroElectric-List Email Forum - | | Use the List Feature Navigator to browse the many List utilities available such as the Email Subscriptions page, Archive Search & Download, 7-Day Browse, Chat, FAQ, Photoshare, and much more:
http://www.matronics.com/Navigator?AeroElectric-List |
|
|
|
Back to top |
|
 |
jluckey(at)pacbell.net Guest
|
Posted: Wed Jan 14, 2015 9:07 am Post subject: UN-FUSED MAIN BUS FEEDER |
|
|
Bob,
Were you able to gain access to an ASTM subscription. I would like to get a look at the http://www.astm.org/Standards/F2245.htm document.
-Jeff
On Wednesday, January 14, 2015 8:32 AM, "Robert L. Nuckolls, III" <nuckolls.bob(at)aeroelectric.com> wrote:
Quote: | In any case, protecting light feeders directly attached to a battery is a good idea. | P.S. Keep in mind that there are numerous ways a failure can take down the main bus. Battery contactor failure. Failure in controls for battery contactor . . . as well as any fault that compromises the main bus feeder. This is one reason why the e-bus evolved to the present day. It's a two-feed bus that not only offers easily accessed, planed reduction in load. It also offers redundancy in source paths that negates risks for loss of main bus. Bob . . .
[quote][b]
| - The Matronics AeroElectric-List Email Forum - | | Use the List Feature Navigator to browse the many List utilities available such as the Email Subscriptions page, Archive Search & Download, 7-Day Browse, Chat, FAQ, Photoshare, and much more:
http://www.matronics.com/Navigator?AeroElectric-List |
|
|
|
Back to top |
|
 |
nuckolls.bob(at)aeroelect Guest
|
Posted: Wed Jan 14, 2015 1:23 pm Post subject: UN-FUSED MAIN BUS FEEDER |
|
|
At 11:06 2015-01-14, you wrote:
Yeah, got a peek at the full document . . . what
is said is rather well written. 33 pages doesn't
cover much from a systems perspective (like part 23)
but they do get into details on weights, handling
qualities and performance. Here's excerpts that
speak to electrical systems . . .
======
Under "Required Equipment"
--------------------------------
A2.6.5 An adequate source of electrical energy for all
installed electrical and radio equipment specified in A2.9.2;
=====================
8.4 Miscellaneous Equipment—Other Than EPU:
----------------------------------------------
8.4.1 If installed, an electrical system shall include a master
switch and overload protection devices (fuses or circuit breakers).
8.4.2 The electric wiring shall be sized according to the load
of each circuit.
8.4.3 The battery installation shall withstand all applicable
inertia loads.
8.4.4 Battery containers shall be vented outside of the
airplane (see 6.5).
======================
A2.9 Electrical Requirements
-----------------------------------------------
A2.9.1 Switches—Each switch must be:
A2.9.1.1 Rated by the switch manufacturer to carry its
circuit’s current;
A2.9.1.2 For circuits containing incandescent lamps, have a
minimum in-rush rating of 15 times the lamp’s continuous
current;
A2.9.1.3 Constructed with enough distance or insulating
material between current carrying parts and the housing so that
vibration in flight will not cause shorting;
A2.9.1.4 Accessible to the pilot;
A2.9.1.5 Labeled as to operation and the circuit controlled;
and
A2.9.1.6 Illuminated in accordance with A2.7.1.
A2.9.2 Circuit Protection Requirements—Circuit overload
protection (fuses or circuit breakers) must:
A2.9.2.1 Be installed on each circuit containing wiring,
equipment, or other components rated for less than the maximum
output of the battery and alternator or generator;
A2.9.2.2 Be appropriately rated for each component installed
on the protected circuit;
A2.9.2.3 Be accessible to and in clear view of the pilot;
A2.9.2.4 Open before the conductor emits smoke; and
A2.9.2.5 Automatic re-set circuit breakers may not be used.
A2.9.3 Electrical Energy Requirements—The total continuous
electrical load may not exceed 80 % of the total rated
generator or alternator output capacity.
A2.9.4 Conductor Requirements—Any wire or other material
intended to conduct electricity must be:
A2.9.4.1 Rated to carry its circuits current;
A2.9.4.2 For wiring rated to 150°C, 600 V minimum;
A2.9.4.3 Constructed with enough distance or insulating
material between current carrying conductors so that vibration
in flight will not cause shorting; and
A2.9.4.4 Where used, insulating material must have, at a
minimum, the equivalent or better properties of either PTFE
-polytetrafluoroethylene (commonly known by the trade name,
TEFLON) or ETFE-(Frequently referred to by the trade name,
TEFZEL) a copolymer of PTFE and of polyethylene including:
(1) Temperature,
(2) Abrasion resistance,
(3) Cut-through resistance,
(4) Chemical resistance,
(5) Flammability,
(6) Smoke generation,
(7) Flexibility,
( Creep (at temperature), and
(9) Arc propagation resistance.
============
All pretty much common sense stuff . . .
Bob . . . [quote][b]
| - The Matronics AeroElectric-List Email Forum - | | Use the List Feature Navigator to browse the many List utilities available such as the Email Subscriptions page, Archive Search & Download, 7-Day Browse, Chat, FAQ, Photoshare, and much more:
http://www.matronics.com/Navigator?AeroElectric-List |
|
|
|
Back to top |
|
 |
peter(at)sportingaero.com Guest
|
Posted: Wed Jan 14, 2015 1:56 pm Post subject: UN-FUSED MAIN BUS FEEDER |
|
|
Does the para below mean that VPX type equipment is not permitted?
Peter
On 14/01/2015 21:22, Robert L. Nuckolls, III wrote:
Quote: | A2.9.2.5 Automatic re-set circuit breakers may not be used.
|
| - The Matronics AeroElectric-List Email Forum - | | Use the List Feature Navigator to browse the many List utilities available such as the Email Subscriptions page, Archive Search & Download, 7-Day Browse, Chat, FAQ, Photoshare, and much more:
http://www.matronics.com/Navigator?AeroElectric-List |
|
|
|
Back to top |
|
 |
jluckey(at)pacbell.net Guest
|
Posted: Wed Jan 14, 2015 2:06 pm Post subject: UN-FUSED MAIN BUS FEEDER |
|
|
Bob,
Thanks for that. A poster on VansAirforce remarked that putting an overload protection device in the feeder to the distribution panel (the wire in question) was specifically prohibited in the ASTM 2245. (which I find hard to believe.)
Did you see any language to that effect?
Thank,
-Jeff
On Wednesday, January 14, 2015 1:33 PM, "Robert L. Nuckolls, III" <nuckolls.bob(at)aeroelectric.com> wrote:
At 11:06 2015-01-14, you wrote:
Yeah, got a peek at the full document . . . what
is said is rather well written. 33 pages doesn't
cover much from a systems perspective (like part 23)
but they do get into details on weights, handling
qualities and performance. Here's excerpts that
speak to electrical systems . . .
======
Under "Required Equipment"
--------------------------------
A2.6.5 An adequate source of electrical energy for all
installed electrical and radio equipment specified in A2.9.2;
=====================
8.4 Miscellaneous Equipment—Other Than EPU:
----------------------------------------------
8.4.1 If installed, an electrical system shall include a master
switch and overload protection devices (fuses or circuit breakers).
8.4.2 The electric wiring shall be sized according to the load
of each circuit.
8.4.3 The battery installation shall withstand all applicable
inertia loads.
8.4.4 Battery containers shall be vented outside of the
airplane (see 6.5).
======================
A2.9 Electrical Requirements
-----------------------------------------------
A2.9.1 Switches—Each switch must be:
A2.9.1.1 Rated by the switch manufacturer to carry its
circuit’s current;
A2.9.1.2 For circuits containing incandescent lamps, have a
minimum in-rush rating of 15 times the lamp’s continuous
current;
A2.9.1.3 Constructed with enough distance or insulating
material between current carrying parts and the housing so that
vibration in flight will not cause shorting;
A2.9.1.4 Accessible to the pilot;
A2.9.1.5 Labeled as to operation and the circuit controlled;
and
A2.9.1.6 Illuminated in accordance with A2.7.1.
A2.9.2 Circuit Protection Requirements—Circuit overload
protection (fuses or circuit breakers) must:
A2.9.2.1 Be installed on each circuit containing wiring,
equipment, or other components rated for less than the maximum
output of the battery and alternator or generator;
A2.9.2.2 Be appropriately rated for each component installed
on the protected circuit;
A2.9.2.3 Be accessible to and in clear view of the pilot;
A2.9.2.4 Open before the conductor emits smoke; and
A2.9.2.5 Automatic re-set circuit breakers may not be used.
A2.9.3 Electrical Energy Requirements—The total continuous
electrical load may not exceed 80 % of the total rated
generator or alternator output capacity.
A2.9.4 Conductor Requirements—Any wire or other material
intended to conduct electricity must be:
A2.9.4.1 Rated to carry its circuits current;
A2.9.4.2 For wiring rated to 150°C, 600 V minimum;
A2.9.4.3 Constructed with enough distance or insulating
material between current carrying conductors so that vibration
in flight will not cause shorting; and
A2.9.4.4 Where used, insulating material must have, at a
minimum, the equivalent or better properties of either PTFE
-polytetrafluoroethylene (commonly known by the trade name,
TEFLON) or ETFE-(Frequently referred to by the trade name,
TEFZEL) a copolymer of PTFE and of polyethylene including:
(1) Temperature,
(2) Abrasion resistance,
(3) Cut-through resistance,
(4) Chemical resistance,
(5) Flammability,
(6) Smoke generation,
(7) Flexibility,
( Creep (at temperature), and
(9) Arc propagation resistance.
============
All pretty much common sense stuff . . .
Bob . . .
[quote]wwwlow" target="_blank" href="http://www.buildersbooks.com/">www.buildersb= * My Pilot Store http://www.matronics.com/Nav========================
" target="_blank" href="http://forums.matronics.com/">http://forums.mat===================
[b]
| - The Matronics AeroElectric-List Email Forum - | | Use the List Feature Navigator to browse the many List utilities available such as the Email Subscriptions page, Archive Search & Download, 7-Day Browse, Chat, FAQ, Photoshare, and much more:
http://www.matronics.com/Navigator?AeroElectric-List |
|
|
|
Back to top |
|
 |
jluckey(at)pacbell.net Guest
|
Posted: Wed Jan 14, 2015 2:17 pm Post subject: UN-FUSED MAIN BUS FEEDER |
|
|
Oops! My paraphrasing was inaccurate. Here is what the other poster said:
"The ASTM specs that the RV-12 is certificated under specifically prohibit the use of of a circuit protector that is not resetable by the pilot. That means the wire highlighted in this discussion can not have a fusible link or any other circuit protection that would actually be capable of preventing a failure in the location that this one was."
Bob, In reading the text you supplied, I did not see anything that supports the above statement. Is there more to the ASTM doc that supports the above?
I'm simply trying to understand what the "Standards" ACTUALLY say. Therefore I'm trying to filter-out hearsay, mis-interpretation, urban legend, & wive's tales.
Again, thanks,
-Jeff
On [quote][b]
| - The Matronics AeroElectric-List Email Forum - | | Use the List Feature Navigator to browse the many List utilities available such as the Email Subscriptions page, Archive Search & Download, 7-Day Browse, Chat, FAQ, Photoshare, and much more:
http://www.matronics.com/Navigator?AeroElectric-List |
|
|
|
Back to top |
|
 |
user9253
Joined: 28 Mar 2008 Posts: 1938 Location: Riley TWP Michigan
|
Posted: Wed Jan 14, 2015 2:27 pm Post subject: Re: UN-FUSED MAIN BUS FEEDER |
|
|
A2.9.2 Does not specifically mention fusible links. Are they considered fuses that must (A2.9.2.3) be accessible to and in clear view of the pilot?
What if a #12 AWG main power feeder were replaced with 8 AWG except for a short section of 12 AWG enclosed in a fire sleeve? Would that meet the letter of the law? Sometimes rules and regulations prohibit using common sense.
Joe
| - The Matronics AeroElectric-List Email Forum - | | Use the List Feature Navigator to browse the many List utilities available such as the Email Subscriptions page, Archive Search & Download, 7-Day Browse, Chat, FAQ, Photoshare, and much more:
http://www.matronics.com/Navigator?AeroElectric-List |
|
_________________ Joe Gores |
|
Back to top |
|
 |
nuckolls.bob(at)aeroelect Guest
|
Posted: Wed Jan 14, 2015 3:01 pm Post subject: UN-FUSED MAIN BUS FEEDER |
|
|
At 16:05 2015-01-14, you wrote:
Quote: | Bob,
Thanks for that. A poster on VansAirforce remarked that putting an overload protection device in the feeder to the distribution panel (the wire in question) was specifically prohibited in the ASTM 2245. (which I find hard to believe.)
Did you see any language to that effect?
Thank,
-Jeff |
Nope . . . in fact, there were words that spoke
specifically to:
A2.9.2.1 Be installed on each circuit containing wiring,
equipment, or other components rated for less than the maximum
output of the battery and alternator or generator;
While poorly worded, I think the intent is similar
to the reasoning for not protecting fat wires
in legacy aircraft.
Reading between the lines, it says that any wire
subject to catastrophic stresses from engine driven
power or battery should be protected. But the
phrase "maximum output of the battery" is
curious . . . most SLVA batteries of any size
are good for 500-1200A in a faulted condition.
Is that the battery's 'rating'? If so, then
one might want to consider fusing a 4AWG
cranking feeder . . . I think I like the FAR23
wording better.
The wording also speaks to equipment and other
components. Do the writers now expect circuit
protection at the bus to look out for potential
faults within a piece of equipment? And where
would the system integrator find data that speaks
to a fault current limit for any failure within
a device?
It would be interesting to know why the wording
in Parts 23 and 25 were inadequate to the new
order . . .
But in any case, I too believe the poster
was in error.
Bob . . . [quote][b]
| - The Matronics AeroElectric-List Email Forum - | | Use the List Feature Navigator to browse the many List utilities available such as the Email Subscriptions page, Archive Search & Download, 7-Day Browse, Chat, FAQ, Photoshare, and much more:
http://www.matronics.com/Navigator?AeroElectric-List |
|
|
|
Back to top |
|
 |
kenryan
Joined: 20 Oct 2009 Posts: 429
|
Posted: Wed Jan 14, 2015 3:47 pm Post subject: UN-FUSED MAIN BUS FEEDER |
|
|
I keep asking myself why I would use a fusible link instead of an inline fuse. So far I am simply not convinced. On Jan 14, 2015 5:33 PM, "user9253" <fransew(at)gmail.com (fransew(at)gmail.com)> wrote:[quote]--> AeroElectric-List message posted by: "user9253" <fransew(at)gmail.com (fransew(at)gmail.com)>
A2.9.2 Does not specifically mention fusible links. Are they considered fuses that must (A2.9.2.3) be accessible to and in clear view of the pilot?
What if a #12 AWG main power feeder were replaced with 8 AWG except for a short section of 12 AWG enclosed in a fire sleeve? Would that meet the letter of the law? Sometimes rules and regulations prohibit using common sense.
Joe
--------
Joe Gores
Read this topic online here:
http://forums.matronics.com/viewtopic.php?p=437014#437014
===========
br> fts!)
r> > com" target="_blank">www.aeroelectric.com
w.buildersbooks.com" target="_blank">www.buildersbooks.com
p.com" target="_blank">www.homebuilthelp.com
e.com" target="_blank">www.mypilotstore.com
" target="_blank">www.mrrace.com
target="_blank">http://www.matronics.com/contribution
     -Matt Dralle, List Admin.
===========
-
Electric-List" target="_blank">http://www.matronics.com/Navigator?AeroElectric-List
===========
FORUMS -
_blank">http://forums.matronics.com
===========
[b]
| - The Matronics AeroElectric-List Email Forum - | | Use the List Feature Navigator to browse the many List utilities available such as the Email Subscriptions page, Archive Search & Download, 7-Day Browse, Chat, FAQ, Photoshare, and much more:
http://www.matronics.com/Navigator?AeroElectric-List |
|
|
|
Back to top |
|
 |
user9253
Joined: 28 Mar 2008 Posts: 1938 Location: Riley TWP Michigan
|
Posted: Wed Jan 14, 2015 4:29 pm Post subject: Re: UN-FUSED MAIN BUS FEEDER |
|
|
Quote: | I keep asking myself why I would use a fusible link instead of an inline fuse. |
I think that fusible links are more robust and less likely to fail than a fuse. However, there are some very robust types of fuses like the ANL. The old style automotive glass fuses were prone to fail because the fuse holders did not make a high pressure contact. Yeah, if I wanted to protect my 12 AWG main feeder from vaporizing, I would install an inline 30 amp ATC fuse. My posting about fusible links was in response to a Van's Aircraft employee who stated that fusible links in the engine compartment were prohibited by ASTM rules. But it seems those rules are ambiguous and open to interpretation.
Joe
| - The Matronics AeroElectric-List Email Forum - | | Use the List Feature Navigator to browse the many List utilities available such as the Email Subscriptions page, Archive Search & Download, 7-Day Browse, Chat, FAQ, Photoshare, and much more:
http://www.matronics.com/Navigator?AeroElectric-List |
|
_________________ Joe Gores |
|
Back to top |
|
 |
jluckey(at)pacbell.net Guest
|
Posted: Wed Jan 14, 2015 5:20 pm Post subject: UN-FUSED MAIN BUS FEEDER |
|
|
Ken,
Regarding a fusible link - There is one reason I can think of that someone might choose a fusible like: Fusible Links are a "slow-blow" kind of animal where a standard fuse is not. If the mission requires a slow-blow device then the Fusible Link might be the right choice. Fusible Links are also cheap.
But I'm with you, my preference is to use Current Limiters like ANL or Littlefuse MIDIs instead of a Fusible Link. But these fuses must be mounted on something...
-Jeff
On Wednesday, January 14, 2015 3:57 PM, Ken Ryan <keninalaska(at)gmail.com> wrote:
I keep asking myself why I would use a fusible link instead of an inline fuse. So far I am simply not convinced.
On Jan 14, 2015 5:33 PM, "user9253" <fransew(at)gmail.com (fransew(at)gmail.com)> wrote:
[quote]--> AeroElectric-List message posted by: "user9253" <fransew(at)gmail.com (fransew(at)gmail.com)>
A2.9.2 Does not specifically mention fusible links. Are they considered fuses that must (A2.9.2.3) be accessible to and in clear view of the pilot?
What if a #12 AWG main power feeder were replaced with 8 AWG except for a short section of 12 AWG enclosed in a fire sleeve? Would that meet the letter of the law? Sometimes rules and regulations prohibit using common sense.
Joe
--------
Joe Gores
Read this topic online here:
http://forums.matronics.com/viewtopic.php?p=437014#437014
===========
br> fts!)
r> > com" target="_blank">www.aeroelectric.com
w.buildersbooks.com" target="_blank">www.buildersbooks.com
p.com" target="_blank">www.homebuilthelp.com
e.com" target="_blank">www.mypilotstore.com
" target="_blank">www.mrrace.com
target="_blank">http://www.matronics.com/contribution
-Matt Dralle, List Admin.
===========
-
Electric-List" target="_blank">http://www.matronics.com/Navigator?AeroElectric-List
===========
FORUMS -
_blank">http://forums.matronics.com
===========
[b]
| - The Matronics AeroElectric-List Email Forum - | | Use the List Feature Navigator to browse the many List utilities available such as the Email Subscriptions page, Archive Search & Download, 7-Day Browse, Chat, FAQ, Photoshare, and much more:
http://www.matronics.com/Navigator?AeroElectric-List |
|
|
|
Back to top |
|
 |
nuckolls.bob(at)aeroelect Guest
|
Posted: Wed Jan 14, 2015 5:55 pm Post subject: UN-FUSED MAIN BUS FEEDER |
|
|
At 17:46 2015-01-14, you wrote:
Quote: | I keep asking myself why I would use a fusible link instead of an inline fuse. So far I am simply not convinced.
On Jan 14, 2015 5:33 PM, "user9253" <fransew(at)gmail.com (fransew(at)gmail.com)> wrote: |
If a FUSE . . . meaning NOT an ANL current limiter,
then pick a fuse that is 2 to 3x larger than the
operational current rating for the wire. I.e. a 12AWG
wire (20A) would want a 60A fuse. This is because fuses
are normally applied in situations where relatively
fast response is desirable . . . not so for feeder
protection.
ANL style devices and fusible links have very LONG
time constants. No nuisance trips of these puppies.
Yet, they will operate to put a box around the
protection event whether inside the housing of
a limiter or under the jacket of a fusible link.
Mechanically, the fusible link is attractive because
it generally looks like and can be treated almost
like wire. Crimped joints on each end. Any other
device is 'lumpy', puts more connections in the
pathway and may need to be mounted to some mechanically
immobile surface.
Bob . . . [quote][b]
| - The Matronics AeroElectric-List Email Forum - | | Use the List Feature Navigator to browse the many List utilities available such as the Email Subscriptions page, Archive Search & Download, 7-Day Browse, Chat, FAQ, Photoshare, and much more:
http://www.matronics.com/Navigator?AeroElectric-List |
|
|
|
Back to top |
|
 |
nuckolls.bob(at)aeroelect Guest
|
Posted: Wed Jan 14, 2015 6:16 pm Post subject: UN-FUSED MAIN BUS FEEDER |
|
|
At 16:17 2015-01-14, you wrote:
Quote: | Oops! My paraphrasing was inaccurate. Here is what the other poster said:
"The ASTM specs that the RV-12 is certificated under specifically
prohibit the use of of a circuit protector that is not resetable by the pilot.
|
Opps . . . yeah, that makes a difference. Can't imagine
why that assertion is part of the spec . . . there's
no foundation in FMEA for the outcome of any given
flight by fiddling with circuit protection in the air.
Quote: | That means the wire highlighted in this discussion can not have a
fusible link or any other circuit protection that would actually be
capable of preventing a failure in the location that this one was."
|
My argument would be that the fusible link or ANL
at the battery contactor is not unlike similar devices
scattered about the airplane on King Airs and
their hot-air cousins . . . and those cannot be reached
by pilots either. Lots of breakers on those airplanes
can't be reached either. These are not systems fuses, they're
a hedge against catastrophic events that either (1) put
every device on that feeder at risk of going dark or (2) the
whole damned airplane at risk of going down very brightly.
I'd let the enforcer of requirements choose . . .
Quote: | Bob, In reading the text you supplied, I did not see anything that
supports the above statement. Is there more to the ASTM doc that
supports the above?
I'm simply trying to understand what the "Standards" ACTUALLY say.
Therefore I'm trying to filter-out hearsay, mis-interpretation,
urban legend, & wive's tales.
|
Understand . . . I think I expressed some misgivings
about the relative goodness of this new 'spec'.
Gee, only 33 pages long, a few years old . . . bet the
guys sitting around the table on this one never
did an FMEA or turned wrenches on airplanes.
Consider AC43-13 . . . DECADES old and sifted by
dozens of high-powered spec writers over the years.
However, when offered to EAA for 'friendly critical review'
release of a major revision was delayed another 18 months
and it was STILL full of holes.
Color this ol' dog skeptical as an outcome of having
watched decades of this stuff run under the bridge.
If it were my airplane, there would be a fusible link
at the battery contactor . . . hidden under the sleeving.
Nobody but me needs to know its there. What does Van's
factory wiring dictate?
Bob . . .
| - The Matronics AeroElectric-List Email Forum - | | Use the List Feature Navigator to browse the many List utilities available such as the Email Subscriptions page, Archive Search & Download, 7-Day Browse, Chat, FAQ, Photoshare, and much more:
http://www.matronics.com/Navigator?AeroElectric-List |
|
|
|
Back to top |
|
 |
|
|
You cannot post new topics in this forum You cannot reply to topics in this forum You cannot edit your posts in this forum You cannot delete your posts in this forum You cannot vote in polls in this forum You cannot attach files in this forum You can download files in this forum
|
Powered by phpBB © 2001, 2005 phpBB Group
|